Filter News
Area of Research
News Topics
- (-) 3-D Printing/Advanced Manufacturing (30)
- (-) Simulation (6)
- Advanced Reactors (13)
- Artificial Intelligence (13)
- Big Data (15)
- Bioenergy (15)
- Biology (17)
- Biomedical (11)
- Biotechnology (3)
- Buildings (17)
- Chemical Sciences (7)
- Clean Water (13)
- Climate Change (20)
- Composites (9)
- Computer Science (39)
- Coronavirus (11)
- Critical Materials (11)
- Cybersecurity (3)
- Decarbonization (7)
- Energy Storage (30)
- Environment (43)
- Exascale Computing (1)
- Frontier (1)
- Fusion (9)
- Grid (20)
- High-Performance Computing (11)
- Hydropower (6)
- Irradiation (2)
- Isotopes (5)
- ITER (3)
- Machine Learning (10)
- Materials (34)
- Materials Science (31)
- Mathematics (1)
- Mercury (3)
- Microscopy (11)
- Molten Salt (5)
- Nanotechnology (12)
- National Security (3)
- Net Zero (1)
- Neutron Science (27)
- Nuclear Energy (18)
- Partnerships (1)
- Physics (4)
- Polymers (8)
- Quantum Computing (4)
- Quantum Science (10)
- Security (1)
- Space Exploration (10)
- Statistics (1)
- Summit (6)
- Sustainable Energy (42)
- Transportation (35)
Media Contacts
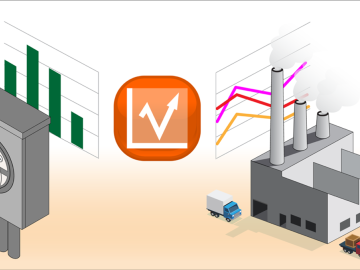
Researchers at ORNL have developed an online tool that offers industrial plants an easier way to track and download information about their energy footprint and carbon emissions.

A multi-lab research team led by ORNL's Paul Kent is developing a computer application called QMCPACK to enable precise and reliable predictions of the fundamental properties of materials critical in energy research.
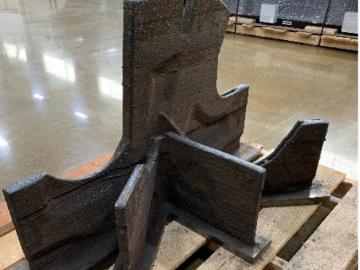
Oak Ridge National Laboratory researchers recently used large-scale additive manufacturing with metal to produce a full-strength steel component for a wind turbine, proving the technique as a viable alternative to

To advance sensor technologies, Oak Ridge National Laboratory researchers studied piezoelectric materials, which convert mechanical stress into electrical energy, to see how they could handle bombardment with energetic neutrons.

Oak Ridge National Laboratory researchers have developed a novel process to manufacture extreme heat resistant carbon-carbon composites. The performance of these materials will be tested in a U.S. Navy rocket that NASA will launch this fall.
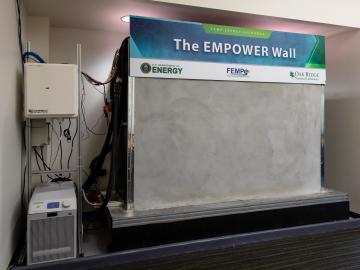
Oak Ridge National Laboratory researchers demonstrated that cooling cost savings could be achieved with a 3D printed concrete smart wall following a three-month field test.

A research team at Oak Ridge National Laboratory have 3D printed a thermal protection shield, or TPS, for a capsule that will launch with the Cygnus cargo spacecraft as part of the supply mission to the International Space Station.
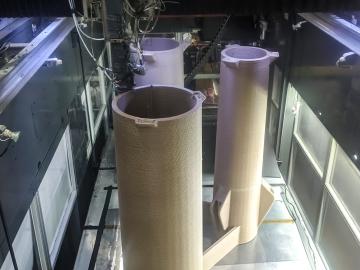
A team of researchers at Oak Ridge National Laboratory demonstrated the ability to additively manufacture power poles from bioderived and recycled materials, which could more quickly restore electricity after natural disasters.
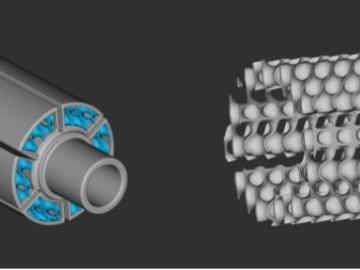
Additive manufacturing can make the design and production of specialized tools for geothermal energy cheaper and more efficient, according to a study by Oak Ridge National Laboratory.
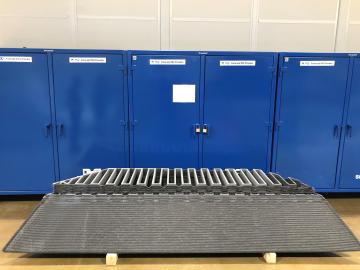
Oak Ridge National Laboratory researchers, in collaboration with Cincinnati Inc., demonstrated the potential for using multimaterials and recycled composites in large-scale applications by 3D printing a mold that replicated a single facet of a