
Filter News
Area of Research
- Advanced Manufacturing (5)
- Biology and Environment (18)
- Clean Energy (29)
- Climate and Environmental Systems (3)
- Computational Engineering (1)
- Computer Science (1)
- Fusion and Fission (2)
- Fusion Energy (6)
- Isotopes (3)
- Materials (23)
- Materials for Computing (8)
- Mathematics (1)
- National Security (2)
- Neutron Science (23)
- Nuclear Science and Technology (4)
- Quantum information Science (1)
- Supercomputing (6)
News Type
News Topics
- (-) Clean Water (13)
- (-) Cybersecurity (3)
- (-) Environment (43)
- (-) Fusion (9)
- (-) Isotopes (5)
- (-) Materials (35)
- (-) Nanotechnology (12)
- (-) Neutron Science (27)
- (-) Physics (4)
- 3-D Printing/Advanced Manufacturing (31)
- Advanced Reactors (13)
- Artificial Intelligence (13)
- Big Data (16)
- Bioenergy (15)
- Biology (17)
- Biomedical (11)
- Biotechnology (3)
- Buildings (19)
- Chemical Sciences (9)
- Climate Change (22)
- Composites (9)
- Computer Science (39)
- Coronavirus (11)
- Critical Materials (12)
- Decarbonization (8)
- Energy Storage (31)
- Exascale Computing (1)
- Frontier (1)
- Grid (20)
- High-Performance Computing (11)
- Hydropower (6)
- Irradiation (2)
- ITER (3)
- Machine Learning (10)
- Materials Science (33)
- Mathematics (1)
- Mercury (3)
- Microscopy (11)
- Molten Salt (5)
- National Security (3)
- Net Zero (1)
- Nuclear Energy (19)
- Partnerships (1)
- Polymers (9)
- Quantum Computing (4)
- Quantum Science (10)
- Security (1)
- Simulation (7)
- Space Exploration (10)
- Statistics (1)
- Summit (6)
- Sustainable Energy (44)
- Transportation (35)
Media Contacts
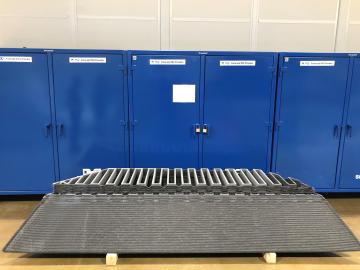
Oak Ridge National Laboratory researchers, in collaboration with Cincinnati Inc., demonstrated the potential for using multimaterials and recycled composites in large-scale applications by 3D printing a mold that replicated a single facet of a
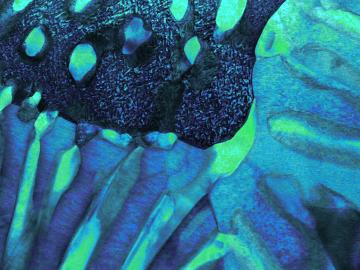
Oak Ridge National Laboratory scientists proved molybdenum titanium carbide, a refractory metal alloy that can withstand extreme temperature environments, can also be crack free and dense when produced with electron beam powder bed fusion.
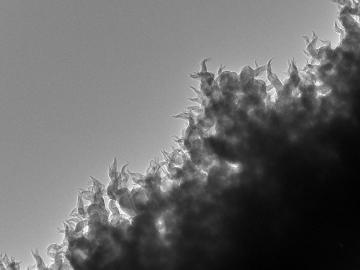
In a new twist to an existing award-winning ORNL technology, researchers have developed an electrocatalyst that enables water and carbon dioxide to be split and the atoms recombined to form higher weight hydrocarbons for gasoline, diesel and jet fuel.
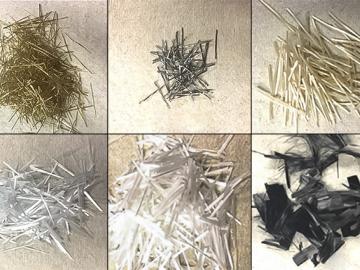
A team of researchers at Oak Ridge National Laboratory and the University of Tennessee have developed a concrete mix that demonstrated high early strength within six hours of mixing, potentially doubling the production capacity for the precast industry.

Researchers at Oak Ridge National Laboratory have identified a statistical relationship between the growth of cities and the spread of paved surfaces like roads and sidewalks. These impervious surfaces impede the flow of water into the ground, affecting the water cycle and, by extension, the climate.
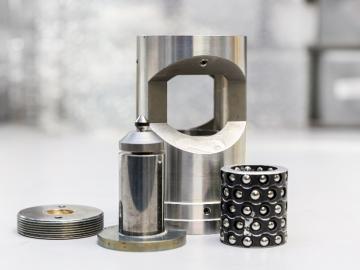
Researchers at Oak Ridge National Laboratory’s Spallation Neutron Source have developed a diamond anvil pressure cell that will enable high-pressure science currently not possible at any other neutron source in the world.
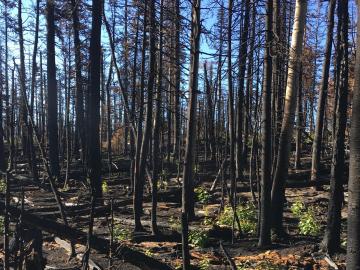
An Oak Ridge National Laboratory research team discovered that aspen saplings emerging after wildfire have less diverse microbiomes and more pathogens in their leaves, providing new insights about how fire affects ecosystem recovery.

A team of Oak Ridge National Laboratory researchers demonstrated that an additively manufactured hot stamping die – a tool used to create car body components – cooled faster than those produced by conventional manufacturing methods.
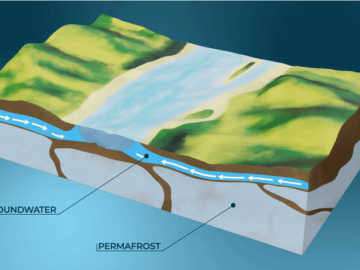
A study by Oak Ridge National Laboratory, the University of Copenhagen, the National Park Service and the U.S. Geological Survey showed that hotter summers and permafrost loss are causing colder water to flow into Arctic streams, which could impact sensitive fish and other wildlife.
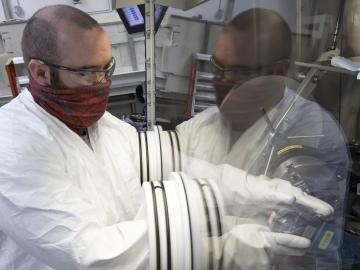
A better way of welding targets for Oak Ridge National Laboratory’s plutonium-238 production has sped up the process and improved consistency and efficiency. This advancement will ultimately benefit the lab’s goal to make enough Pu-238 – the isotope that powers NASA’s deep space missions – to yield 1.5 kilograms of plutonium oxide annually by 2026.