Filter News
Area of Research
News Topics
- (-) Composites (9)
- (-) Materials (35)
- (-) Space Exploration (10)
- 3-D Printing/Advanced Manufacturing (31)
- Advanced Reactors (13)
- Artificial Intelligence (13)
- Big Data (15)
- Bioenergy (15)
- Biology (17)
- Biomedical (11)
- Biotechnology (3)
- Buildings (18)
- Chemical Sciences (8)
- Clean Water (13)
- Climate Change (21)
- Computer Science (39)
- Coronavirus (11)
- Critical Materials (12)
- Cybersecurity (3)
- Decarbonization (8)
- Energy Storage (31)
- Environment (43)
- Exascale Computing (1)
- Frontier (1)
- Fusion (9)
- Grid (20)
- High-Performance Computing (11)
- Hydropower (6)
- Irradiation (2)
- Isotopes (5)
- ITER (3)
- Machine Learning (10)
- Materials Science (33)
- Mathematics (1)
- Mercury (3)
- Microscopy (11)
- Molten Salt (5)
- Nanotechnology (12)
- National Security (3)
- Net Zero (1)
- Neutron Science (27)
- Nuclear Energy (18)
- Partnerships (1)
- Physics (4)
- Polymers (9)
- Quantum Computing (4)
- Quantum Science (10)
- Security (1)
- Simulation (6)
- Statistics (1)
- Summit (6)
- Sustainable Energy (44)
- Transportation (35)
Media Contacts
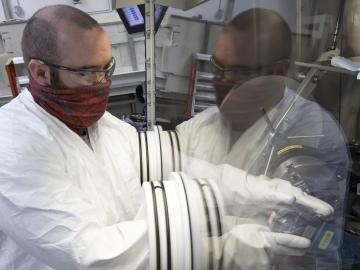
A better way of welding targets for Oak Ridge National Laboratory’s plutonium-238 production has sped up the process and improved consistency and efficiency. This advancement will ultimately benefit the lab’s goal to make enough Pu-238 – the isotope that powers NASA’s deep space missions – to yield 1.5 kilograms of plutonium oxide annually by 2026.

Collaborators at Oak Ridge National Laboratory and the University of Tennessee Health Science Center are developing a breath-sampling whistle that could make COVID-19 screening easy to do at home.

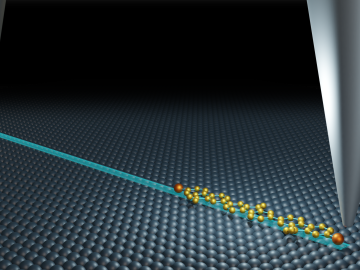
Oak Ridge National Laboratory’s Center for Nanophase Materials Sciences contributed to a groundbreaking experiment published in Science that tracks the real-time transport of individual molecules.
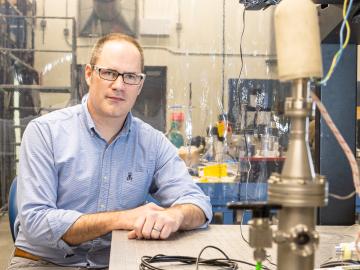
If humankind reaches Mars this century, an Oak Ridge National Laboratory-developed experiment testing advanced materials for spacecraft may play a key role.

A team including Oak Ridge National Laboratory and University of Tennessee researchers demonstrated a novel 3D printing approach called Z-pinning that can increase the material’s strength and toughness by more than three and a half times compared to conventional additive manufacturing processes.

Using the Titan supercomputer at Oak Ridge National Laboratory, a team of astrophysicists created a set of galactic wind simulations of the highest resolution ever performed. The simulations will allow researchers to gather and interpret more accurate, detailed data that elucidates how galactic winds affect the formation and evolution of galaxies.
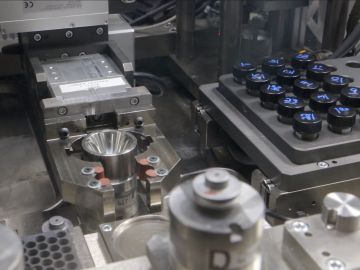
By automating the production of neptunium oxide-aluminum pellets, Oak Ridge National Laboratory scientists have eliminated a key bottleneck when producing plutonium-238 used by NASA to fuel deep space exploration.

A shield assembly that protects an instrument measuring ion and electron fluxes for a NASA mission to touch the Sun was tested in extreme experimental environments at Oak Ridge National Laboratory—and passed with flying colors. Components aboard Parker Solar Probe, which will endure th...
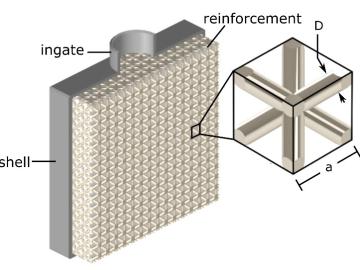
A new manufacturing method created by Oak Ridge National Laboratory and Rice University combines 3D printing with traditional casting to produce damage-tolerant components composed of multiple materials. Composite components made by pouring an aluminum alloy over a printed steel lattice showed an order of magnitude greater damage tolerance than aluminum alone.