
Filter News
Area of Research
- (-) Advanced Manufacturing (22)
- (-) National Security (12)
- (-) Neutron Science (22)
- Biology and Environment (64)
- Biology and Soft Matter (1)
- Building Technologies (1)
- Clean Energy (167)
- Climate and Environmental Systems (2)
- Computational Biology (1)
- Computational Engineering (2)
- Computer Science (3)
- Electricity and Smart Grid (1)
- Energy Sciences (1)
- Functional Materials for Energy (2)
- Fusion and Fission (9)
- Fusion Energy (2)
- Isotope Development and Production (1)
- Isotopes (27)
- Materials (73)
- Materials for Computing (11)
- Mathematics (1)
- Nuclear Science and Technology (12)
- Supercomputing (90)
News Topics
- (-) 3-D Printing/Advanced Manufacturing (28)
- (-) Climate Change (5)
- (-) Energy Storage (8)
- (-) Frontier (2)
- (-) Space Exploration (4)
- (-) Summit (7)
- Advanced Reactors (3)
- Artificial Intelligence (19)
- Big Data (8)
- Bioenergy (10)
- Biology (9)
- Biomedical (13)
- Biotechnology (2)
- Buildings (1)
- Chemical Sciences (4)
- Clean Water (2)
- Composites (4)
- Computer Science (32)
- Coronavirus (10)
- Cybersecurity (20)
- Decarbonization (4)
- Environment (13)
- Exascale Computing (1)
- Fossil Energy (1)
- Fusion (3)
- Grid (6)
- High-Performance Computing (6)
- Machine Learning (16)
- Materials (20)
- Materials Science (28)
- Mathematics (1)
- Microscopy (3)
- Nanotechnology (11)
- National Security (34)
- Neutron Science (99)
- Nuclear Energy (9)
- Partnerships (4)
- Physics (10)
- Polymers (1)
- Quantum Computing (1)
- Quantum Science (8)
- Security (12)
- Simulation (1)
- Sustainable Energy (9)
- Transformational Challenge Reactor (1)
- Transportation (7)
Media Contacts
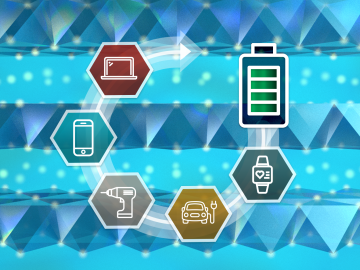
Two of the researchers who share the Nobel Prize in Chemistry announced Wednesday—John B. Goodenough of the University of Texas at Austin and M. Stanley Whittingham of Binghamton University in New York—have research ties to ORNL.

A team including Oak Ridge National Laboratory and University of Tennessee researchers demonstrated a novel 3D printing approach called Z-pinning that can increase the material’s strength and toughness by more than three and a half times compared to conventional additive manufacturing processes.

Using additive manufacturing, scientists experimenting with tungsten at Oak Ridge National Laboratory hope to unlock new potential of the high-performance heat-transferring material used to protect components from the plasma inside a fusion reactor. Fusion requires hydrogen isotopes to reach millions of degrees.

OAK RIDGE, Tenn., May 8, 2019—Oak Ridge National Laboratory and Lincoln Electric (NASDAQ: LECO) announced their continued collaboration on large-scale, robotic additive manufacturing technology at the Department of Energy’s Advanced Manufacturing InnovationXLab Summit.
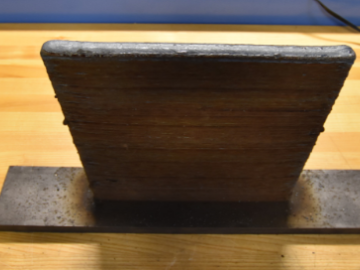
A novel additive manufacturing method developed by researchers at Oak Ridge National Laboratory could be a promising alternative for low-cost, high-quality production of large-scale metal parts with less material waste.

Ionic conduction involves the movement of ions from one location to another inside a material. The ions travel through point defects, which are irregularities in the otherwise consistent arrangement of atoms known as the crystal lattice. This sometimes sluggish process can limit the performance and efficiency of fuel cells, batteries, and other energy storage technologies.
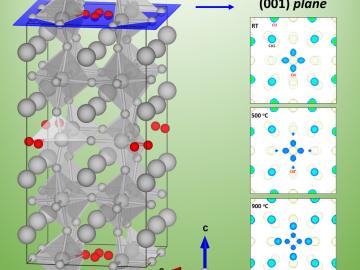
A University of South Carolina research team is investigating the oxygen reduction performance of energy conversion materials called perovskites by using neutron diffraction at Oak Ridge National Laboratory’s Spallation Neutron Source.
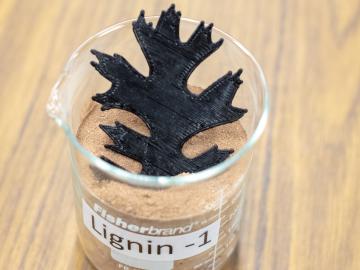
Scientists at the Department of Energy’s Oak Ridge National Laboratory have created a recipe for a renewable 3D printing feedstock that could spur a profitable new use for an intractable biorefinery byproduct: lignin.
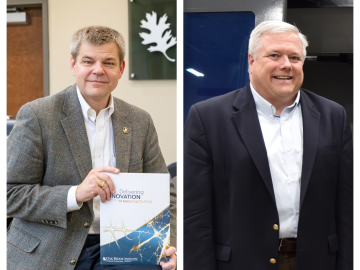
Two leaders in US manufacturing innovation, Thomas Kurfess and Scott Smith, are joining the Department of Energy’s Oak Ridge National Laboratory to support its pioneering research in advanced manufacturing.

The construction industry may soon benefit from 3D printed molds to make concrete facades, promising lower cost and production time. Researchers at Oak Ridge National Laboratory are evaluating the performance of 3D printed molds used to precast concrete facades in a 42-story buildin...