Filter News
Area of Research
- (-) Materials (30)
- (-) National Security (14)
- Advanced Manufacturing (22)
- Biology and Environment (18)
- Building Technologies (1)
- Clean Energy (83)
- Computational Biology (1)
- Computational Engineering (1)
- Computer Science (6)
- Electricity and Smart Grid (1)
- Functional Materials for Energy (1)
- Fusion and Fission (4)
- Fusion Energy (1)
- Materials for Computing (4)
- Neutron Science (11)
- Nuclear Science and Technology (4)
- Supercomputing (40)
News Topics
- (-) 3-D Printing/Advanced Manufacturing (25)
- (-) Artificial Intelligence (21)
- Advanced Reactors (5)
- Big Data (7)
- Bioenergy (14)
- Biology (8)
- Biomedical (8)
- Biotechnology (1)
- Buildings (6)
- Chemical Sciences (32)
- Clean Water (3)
- Climate Change (9)
- Composites (9)
- Computer Science (33)
- Coronavirus (6)
- Critical Materials (13)
- Cybersecurity (21)
- Decarbonization (9)
- Energy Storage (35)
- Environment (20)
- Exascale Computing (2)
- Frontier (3)
- Fusion (8)
- Grid (11)
- High-Performance Computing (8)
- Irradiation (1)
- Isotopes (13)
- ITER (1)
- Machine Learning (16)
- Materials (74)
- Materials Science (78)
- Mathematics (1)
- Microscopy (27)
- Molten Salt (3)
- Nanotechnology (39)
- National Security (34)
- Net Zero (1)
- Neutron Science (35)
- Nuclear Energy (21)
- Partnerships (14)
- Physics (29)
- Polymers (17)
- Quantum Computing (3)
- Quantum Science (12)
- Renewable Energy (1)
- Security (11)
- Simulation (2)
- Space Exploration (2)
- Summit (4)
- Sustainable Energy (16)
- Transformational Challenge Reactor (3)
- Transportation (16)
Media Contacts
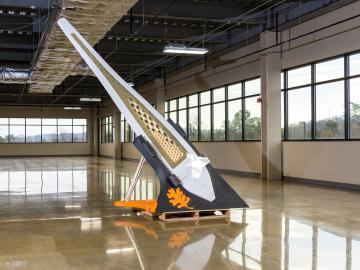
In the shifting landscape of global manufacturing, American ingenuity is once again giving U.S companies an edge with radical productivity improvements as a result of advanced materials and robotic systems developed at the Department of Energy’s Manufacturing Demonstration Facility (MDF) at Oak Ridge National Laboratory.
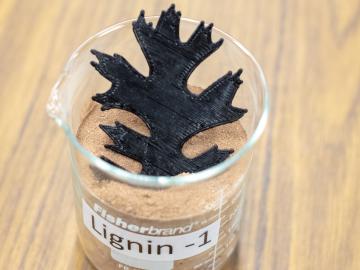
Scientists at the Department of Energy’s Oak Ridge National Laboratory have created a recipe for a renewable 3D printing feedstock that could spur a profitable new use for an intractable biorefinery byproduct: lignin.

Oak Ridge National Laboratory scientists have improved a mixture of materials used to 3D print permanent magnets with increased density, which could yield longer lasting, better performing magnets for electric motors, sensors and vehicle applications. Building on previous research, ...
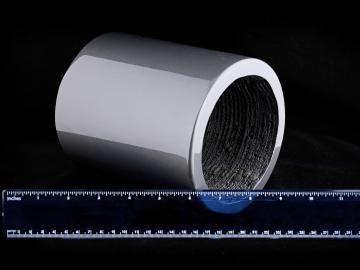
Researchers at the Department of Energy’s Oak Ridge National Laboratory have demonstrated that permanent magnets produced by additive manufacturing can outperform bonded magnets made using traditional techniques while conserving critical materials. Scientists fabric...