Filter News
Area of Research
News Topics
- (-) Advanced Reactors (9)
- 3-D Printing/Advanced Manufacturing (89)
- Artificial Intelligence (13)
- Big Data (7)
- Bioenergy (30)
- Biology (12)
- Biomedical (10)
- Biotechnology (4)
- Buildings (36)
- Chemical Sciences (32)
- Clean Water (10)
- Climate Change (23)
- Composites (19)
- Computer Science (36)
- Coronavirus (14)
- Critical Materials (18)
- Cybersecurity (10)
- Decarbonization (34)
- Energy Storage (86)
- Environment (64)
- Exascale Computing (3)
- Fossil Energy (2)
- Frontier (3)
- Fusion (7)
- Grid (41)
- High-Performance Computing (9)
- Hydropower (2)
- Irradiation (1)
- Isotopes (13)
- ITER (1)
- Machine Learning (10)
- Materials (94)
- Materials Science (90)
- Mathematics (3)
- Mercury (3)
- Microelectronics (1)
- Microscopy (29)
- Molten Salt (3)
- Nanotechnology (41)
- National Security (6)
- Net Zero (3)
- Neutron Science (42)
- Nuclear Energy (22)
- Partnerships (15)
- Physics (29)
- Polymers (21)
- Quantum Computing (3)
- Quantum Science (12)
- Renewable Energy (1)
- Security (7)
- Simulation (4)
- Space Exploration (5)
- Statistics (1)
- Summit (6)
- Sustainable Energy (71)
- Transformational Challenge Reactor (5)
- Transportation (69)
Media Contacts

Anne Campbell, a researcher at ORNL, recently won the Young Leaders Professional Development Award from the Minerals, Metals & Materials Society, or TMS, and has been chosen as the first recipient of the Young Leaders International Scholar Program award from TMS and the Korean Institute of Metals and Materials, or KIM.

ORNL and the Tennessee Valley Authority, or TVA, are joining forces to advance decarbonization technologies from discovery through deployment through a new memorandum of understanding, or MOU.

ORNL, TVA and TNECD were recognized by the Federal Laboratory Consortium for their impactful partnership that resulted in a record $2.3 billion investment by Ultium Cells, a General Motors and LG Energy Solution joint venture, to build a battery cell manufacturing plant in Spring Hill, Tennessee.
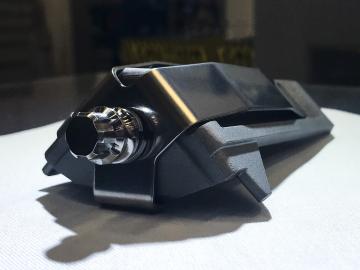
Four first-of-a-kind 3D-printed fuel assembly brackets, produced at the Department of Energy’s Manufacturing Demonstration Facility at Oak Ridge National Laboratory, have been installed and are now under routine operating
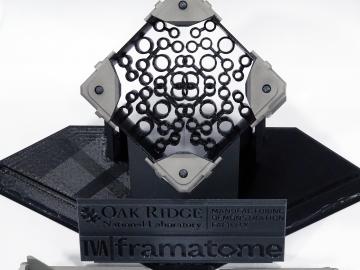
The Transformational Challenge Reactor, or TCR, a microreactor built using 3D printing and other new advanced technologies, could be operational by 2024.

The Department of Energy’s Office of Science has selected three Oak Ridge National Laboratory scientists for Early Career Research Program awards.
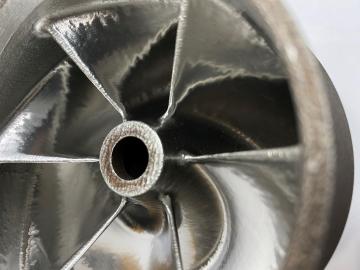
Scientists at the Department of Energy Manufacturing Demonstration Facility at ORNL have their eyes on the prize: the Transformational Challenge Reactor, or TCR, a microreactor built using 3D printing and other new approaches that will be up and running by 2023.

Researchers at the Department of Energy’s Oak Ridge National Laboratory are refining their design of a 3D-printed nuclear reactor core, scaling up the additive manufacturing process necessary to build it, and developing methods

Using additive manufacturing, scientists experimenting with tungsten at Oak Ridge National Laboratory hope to unlock new potential of the high-performance heat-transferring material used to protect components from the plasma inside a fusion reactor. Fusion requires hydrogen isotopes to reach millions of degrees.