
Filter News
Area of Research
- (-) Clean Energy (21)
- (-) Materials (11)
- Advanced Manufacturing (3)
- Biology and Environment (15)
- Computational Biology (1)
- Computational Engineering (1)
- Computer Science (1)
- Fusion and Fission (1)
- Fusion Energy (1)
- Materials for Computing (2)
- National Security (2)
- Neutron Science (7)
- Supercomputing (42)
News Topics
- (-) Composites (19)
- (-) Summit (6)
- 3-D Printing/Advanced Manufacturing (89)
- Advanced Reactors (9)
- Artificial Intelligence (13)
- Big Data (7)
- Bioenergy (30)
- Biology (12)
- Biomedical (10)
- Biotechnology (4)
- Buildings (36)
- Chemical Sciences (33)
- Clean Water (10)
- Climate Change (23)
- Computer Science (36)
- Coronavirus (14)
- Critical Materials (19)
- Cybersecurity (10)
- Decarbonization (34)
- Energy Storage (86)
- Environment (64)
- Exascale Computing (3)
- Fossil Energy (2)
- Frontier (3)
- Fusion (7)
- Grid (41)
- High-Performance Computing (9)
- Hydropower (2)
- Irradiation (1)
- Isotopes (13)
- ITER (1)
- Machine Learning (10)
- Materials (94)
- Materials Science (90)
- Mathematics (3)
- Mercury (3)
- Microelectronics (1)
- Microscopy (29)
- Molten Salt (3)
- Nanotechnology (41)
- National Security (6)
- Net Zero (3)
- Neutron Science (42)
- Nuclear Energy (22)
- Partnerships (16)
- Physics (29)
- Polymers (21)
- Quantum Computing (3)
- Quantum Science (12)
- Renewable Energy (1)
- Security (7)
- Simulation (4)
- Space Exploration (5)
- Statistics (1)
- Sustainable Energy (71)
- Transformational Challenge Reactor (5)
- Transportation (69)
Media Contacts

A team including Oak Ridge National Laboratory and University of Tennessee researchers demonstrated a novel 3D printing approach called Z-pinning that can increase the material’s strength and toughness by more than three and a half times compared to conventional additive manufacturing processes.
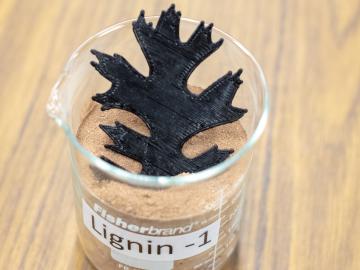
Scientists at the Department of Energy’s Oak Ridge National Laboratory have created a recipe for a renewable 3D printing feedstock that could spur a profitable new use for an intractable biorefinery byproduct: lignin.
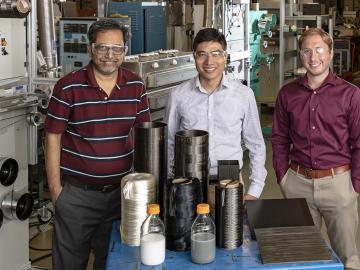
Carbon fiber composites—lightweight and strong—are great structural materials for automobiles, aircraft and other transportation vehicles. They consist of a polymer matrix, such as epoxy, into which reinforcing carbon fibers have been embedded. Because of differences in the mecha...
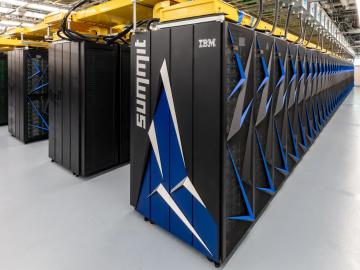
The U.S. Department of Energy’s Oak Ridge National Laboratory today unveiled Summit as the world’s most powerful and smartest scientific supercomputer.
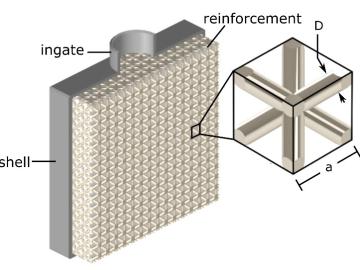
A new manufacturing method created by Oak Ridge National Laboratory and Rice University combines 3D printing with traditional casting to produce damage-tolerant components composed of multiple materials. Composite components made by pouring an aluminum alloy over a printed steel lattice showed an order of magnitude greater damage tolerance than aluminum alone.