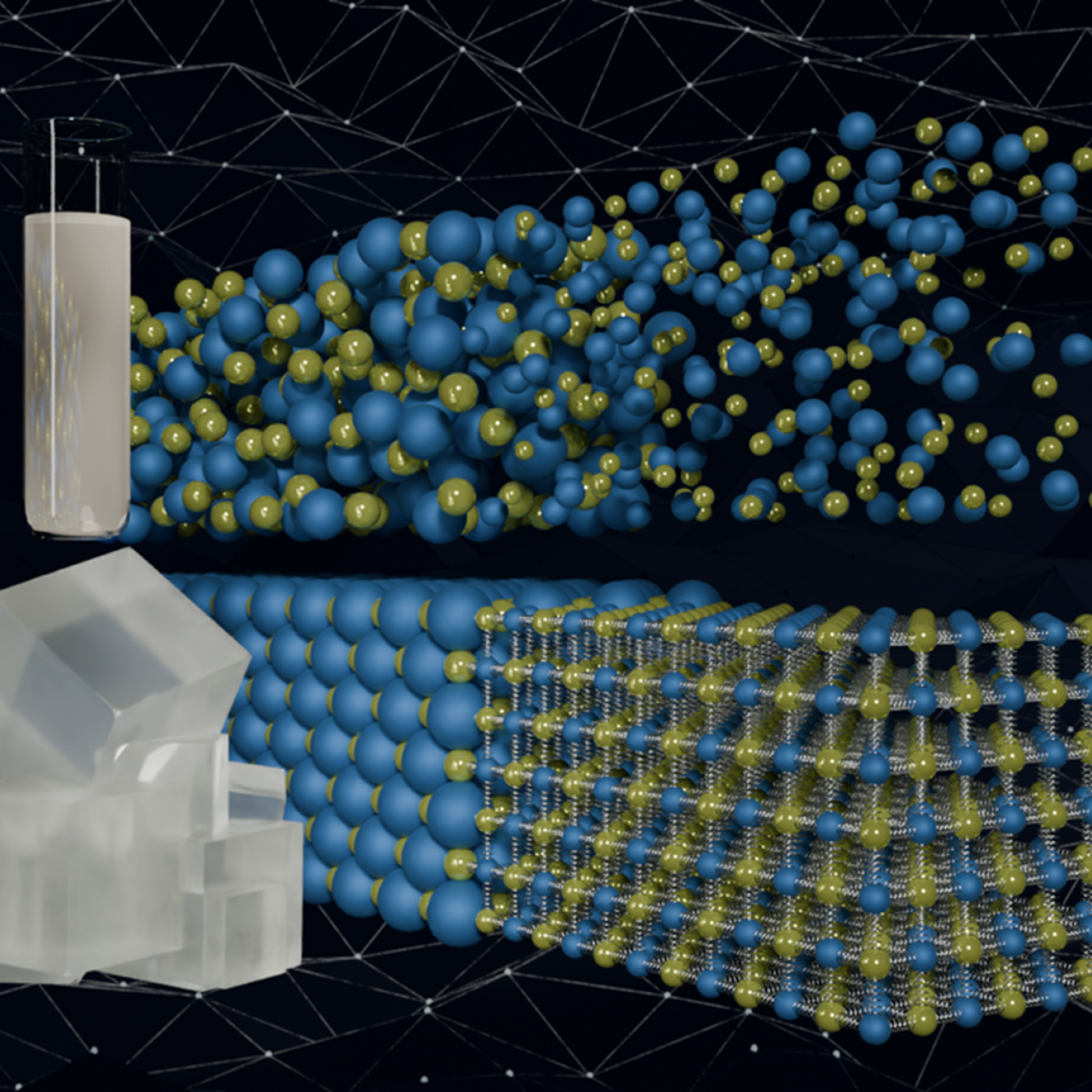
Filter News
Area of Research
- Advanced Manufacturing (22)
- Biology and Environment (23)
- Building Technologies (1)
- Computational Engineering (1)
- Computer Science (6)
- Electricity and Smart Grid (1)
- Energy Science (148)
- Energy Sciences (1)
- Functional Materials for Energy (2)
- Fusion and Fission (7)
- Fusion Energy (1)
- Isotopes (1)
- Materials (68)
- Materials for Computing (7)
- National Security (16)
- Neutron Science (14)
- Nuclear Science and Technology (4)
- Supercomputing (27)
News Topics
- (-) 3-D Printing/Advanced Manufacturing (146)
- (-) Critical Materials (29)
- (-) Energy Storage (114)
- (-) Machine Learning (68)
- Advanced Reactors (40)
- Artificial Intelligence (131)
- Big Data (79)
- Bioenergy (112)
- Biology (128)
- Biomedical (73)
- Biotechnology (39)
- Buildings (74)
- Chemical Sciences (86)
- Clean Water (33)
- Composites (35)
- Computer Science (226)
- Coronavirus (48)
- Cybersecurity (35)
- Education (5)
- Element Discovery (1)
- Emergency (4)
- Environment (218)
- Exascale Computing (67)
- Fossil Energy (8)
- Frontier (64)
- Fusion (66)
- Grid (74)
- High-Performance Computing (130)
- Hydropower (12)
- Irradiation (3)
- Isotopes (62)
- ITER (9)
- Materials (157)
- Materials Science (158)
- Mathematics (12)
- Mercury (12)
- Microelectronics (4)
- Microscopy (56)
- Molten Salt (10)
- Nanotechnology (64)
- National Security (86)
- Neutron Science (171)
- Nuclear Energy (122)
- Partnerships (68)
- Physics (69)
- Polymers (35)
- Quantum Computing (53)
- Quantum Science (92)
- Security (31)
- Simulation (65)
- Software (1)
- Space Exploration (26)
- Statistics (4)
- Summit (71)
- Transportation (103)
Media Contacts

Researchers have developed and 3D printed the lightest crack-free alloy capable of operating without melting at temperatures above 2,400 degrees Fahrenheit, which could enable additively manufactured turbine blades to better handle extreme temperatures, reducing the carbon footprint of gas turbine engines such as those used in airplanes.

The Advanced Plant Phenotyping Laboratory at ORNL utilizes robotics, multi-modal imaging, and AI to enhance understanding of plant genetics and interactions with microbes. It aims to connect genes to traits for advancements in bioenergy, agriculture, and climate resilience. Senior scientist Larry York highlights the lab's capabilities and the insights from a new digital underground imaging system to improve biomass feedstocks for bioenergy and carbon storage.

To bridge the gap between experimental facilities and supercomputers, experts from SLAC National Accelerator Laboratory are teaming up with other DOE national laboratories to build a new data streaming pipeline. The pipeline will allow researchers to send their data to the nation’s leading computing centers for analysis in real time even as their experiments are taking place.

ORNL researchers were honored with a prestigious ACE Award for Composites Excellence by the American Composites Manufacturers Association. The team won the “innovation in green composites design” prize for creating a fully recyclable, lightweight wind turbine blade tip that incorporates low-cost carbon fiber and conductive coating for enhanced protection against lightning strikes.

Researchers at ORNL are using advanced manufacturing techniques to revitalize the domestic production of very large metal parts that weigh at least 10,000 pounds each and are necessary for a variety of industries, including energy.
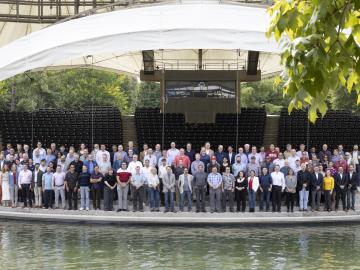
The Smoky Mountain Computational Sciences and Engineering Conference, or SMC24, entered its third decade with the 21st annual gathering in East Tennessee.
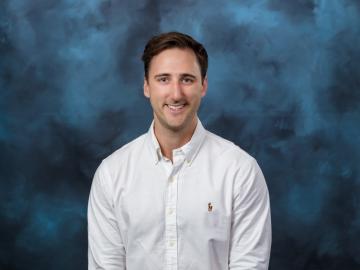
Justin West, an advanced machining and machine tool researcher at ORNL, has been selected as a recipient of the 2024 30 Under 30 award by the Society of Manufacturing Engineers.

Daryl Yang is coupling his science and engineering expertise to devise new ways to measure significant changes going on in the Arctic, a region that’s warming nearly four times faster than other parts of the planet. The remote sensing technologies and modeling tools he develops and leverages for the Next-Generation Ecosystem Experiments in the Arctic project, or NGEE Arctic, help improve models of the ecosystem to better inform decision-making as the landscape changes.
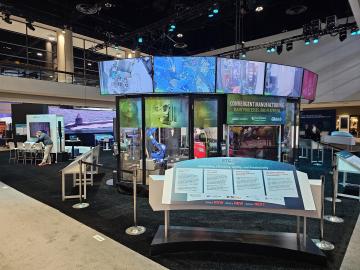
A new convergent manufacturing platform, developed in only five months at the Department of Energy’s Oak Ridge National Laboratory, is debuting at the International Manufacturing Technology Show, or IMTS, in Chicago, Sept. 9–12, 2024.

A team led by scientists at ORNL identified and demonstrated a method to process a plant-based material called nanocellulose that reduced energy needs by a whopping 21%, using simulations on the lab’s supercomputers and follow-on analysis.