
Filter News
Area of Research
- Advanced Manufacturing (22)
- Biology and Environment (32)
- Building Technologies (4)
- Clean Energy (127)
- Climate and Environmental Systems (1)
- Computational Biology (1)
- Computational Engineering (3)
- Computer Science (15)
- Electricity and Smart Grid (1)
- Functional Materials for Energy (1)
- Fusion and Fission (6)
- Fusion Energy (3)
- Isotopes (1)
- Materials (41)
- Materials for Computing (10)
- Mathematics (1)
- National Security (22)
- Neutron Science (18)
- Nuclear Science and Technology (6)
- Quantum information Science (6)
- Supercomputing (110)
News Topics
- (-) 3-D Printing/Advanced Manufacturing (124)
- (-) Buildings (57)
- (-) Computer Science (192)
- (-) Exascale Computing (38)
- Advanced Reactors (34)
- Artificial Intelligence (94)
- Big Data (57)
- Bioenergy (92)
- Biology (100)
- Biomedical (59)
- Biotechnology (22)
- Chemical Sciences (66)
- Clean Water (30)
- Climate Change (101)
- Composites (28)
- Coronavirus (46)
- Critical Materials (27)
- Cybersecurity (35)
- Decarbonization (80)
- Education (4)
- Element Discovery (1)
- Emergency (2)
- Energy Storage (109)
- Environment (196)
- Fossil Energy (6)
- Frontier (43)
- Fusion (55)
- Grid (65)
- High-Performance Computing (87)
- Hydropower (11)
- Irradiation (3)
- Isotopes (53)
- ITER (7)
- Machine Learning (48)
- Materials (144)
- Materials Science (141)
- Mathematics (9)
- Mercury (12)
- Microelectronics (3)
- Microscopy (51)
- Molten Salt (8)
- Nanotechnology (60)
- National Security (65)
- Net Zero (14)
- Neutron Science (131)
- Nuclear Energy (109)
- Partnerships (46)
- Physics (62)
- Polymers (33)
- Quantum Computing (35)
- Quantum Science (69)
- Renewable Energy (2)
- Security (24)
- Simulation (49)
- Software (1)
- Space Exploration (25)
- Statistics (3)
- Summit (58)
- Sustainable Energy (129)
- Transformational Challenge Reactor (7)
- Transportation (97)
Media Contacts

Two ORNL teams recently completed Cohort 18 of Energy I-Corps, an immersive two-month training program where the scientists define their technology’s value propositions, conduct stakeholder discovery interviews and develop viable market pathways.

Power companies and electric grid developers turn to simulation tools as they attempt to understand how modern equipment will be affected by rapidly unfolding events in a complex grid.

Brittany Rodriguez never imagined she would pursue a science career at a Department of Energy national laboratory. However, after some encouraging words from her mother, input from key mentors at the University of Texas Rio Grande Valley, or UTRGV, and a lot of hard work, Rodriguez landed at DOE’s Manufacturing Demonstration Facility, or MDF, at Oak Ridge National Laboratory.
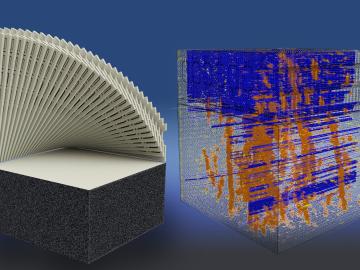
The Department of Energy’s Oak Ridge National Laboratory has publicly released a new set of additive manufacturing data that industry and researchers can use to evaluate and improve the quality of 3D-printed components. The breadth of the datasets can significantly boost efforts to verify the quality of additively manufactured parts using only information gathered during printing, without requiring expensive and time-consuming post-production analysis.

Researchers conduct largest, most accurate molecular dynamics simulations to date of two million correlated electrons using Frontier, the world’s fastest supercomputer. The simulation, which exceed an exaflop using full double precision, is 1,000 times greater in size and speed than any quantum chemistry simulation of it's kind.

In the wet, muddy places where America’s rivers and lands meet the sea, scientists from the Department of Energy’s Oak Ridge National Laboratory are unearthing clues to better understand how these vital landscapes are evolving under climate change.
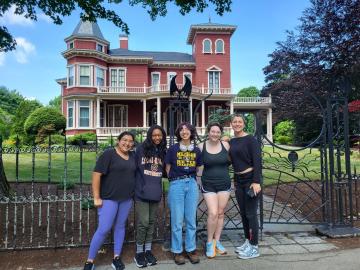
Participants in the SM2ART Research Experience for Undergraduates program got the chance to see what life is like in a research setting. REU participant Brianna Greer studied banana fibers as a reinforcing material in making lightweight parts for cars and bicycles.

Oak Ridge National Laboratory scientists have developed a method leveraging artificial intelligence to accelerate the identification of environmentally friendly solvents for industrial carbon capture, biomass processing, rechargeable batteries and other applications.

Advanced materials research to enable energy-efficient, cost-competitive and environmentally friendly technologies for the United States and Japan is the goal of a memorandum of understanding, or MOU, between the Department of Energy’s Oak Ridge National Laboratory and Japan’s National Institute of Materials Science.

Researchers at ORNL have developed the first additive manufacturing slicing computer application to simultaneously speed and simplify digital conversion of accurate, large-format three-dimensional parts in a factory production setting.