
Filter News
Area of Research
- Advanced Manufacturing (22)
- Biology and Environment (19)
- Building Technologies (4)
- Clean Energy (110)
- Computer Science (1)
- Electricity and Smart Grid (1)
- Functional Materials for Energy (1)
- Fusion and Fission (26)
- Fusion Energy (13)
- Materials (32)
- Materials for Computing (4)
- National Security (4)
- Neutron Science (7)
- Nuclear Science and Technology (12)
- Renewable Energy (1)
- Supercomputing (10)
News Topics
- (-) 3-D Printing/Advanced Manufacturing (121)
- (-) Buildings (57)
- (-) Fusion (54)
- (-) Hydropower (11)
- Advanced Reactors (34)
- Artificial Intelligence (91)
- Big Data (53)
- Bioenergy (91)
- Biology (98)
- Biomedical (58)
- Biotechnology (22)
- Chemical Sciences (63)
- Clean Water (29)
- Climate Change (99)
- Composites (26)
- Computer Science (187)
- Coronavirus (46)
- Critical Materials (26)
- Cybersecurity (35)
- Decarbonization (79)
- Education (4)
- Element Discovery (1)
- Emergency (2)
- Energy Storage (108)
- Environment (194)
- Exascale Computing (37)
- Fossil Energy (5)
- Frontier (42)
- Grid (62)
- High-Performance Computing (84)
- Irradiation (3)
- Isotopes (53)
- ITER (7)
- Machine Learning (47)
- Materials (144)
- Materials Science (140)
- Mathematics (7)
- Mercury (12)
- Microelectronics (3)
- Microscopy (51)
- Molten Salt (8)
- Nanotechnology (60)
- National Security (61)
- Net Zero (13)
- Neutron Science (131)
- Nuclear Energy (108)
- Partnerships (44)
- Physics (61)
- Polymers (33)
- Quantum Computing (34)
- Quantum Science (69)
- Renewable Energy (2)
- Security (24)
- Simulation (47)
- Software (1)
- Space Exploration (25)
- Statistics (3)
- Summit (57)
- Sustainable Energy (125)
- Transformational Challenge Reactor (7)
- Transportation (97)
Media Contacts

ORNL researchers have identified a mechanism in a 3D-printed alloy – termed “load shuffling” — that could enable the design of better-performing lightweight materials for vehicles.

Three researchers at ORNL have been named ORNL Corporate Fellows in recognition of significant career accomplishments and continued leadership in their scientific fields.

The presence of minerals called ash in plants makes little difference to the fitness of new naturally derived compound materials designed for additive manufacturing, an Oak Ridge National Laboratory-led team found.

Researchers at Oak Ridge National Laboratory have identified a key need for future hydropower innovations – full-scale testing – to better inform developers and operators before making major investments.
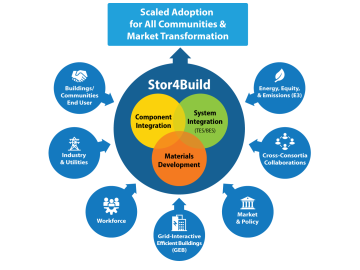
Stor4Build is a new consortium focused on energy storage for buildings that will accelerate the growth, optimization and deployment of storage technologies.

Oak Ridge National Laboratory scientists designed a recyclable polymer for carbon-fiber composites to enable circular manufacturing of parts that boost energy efficiency in automotive, wind power and aerospace applications.
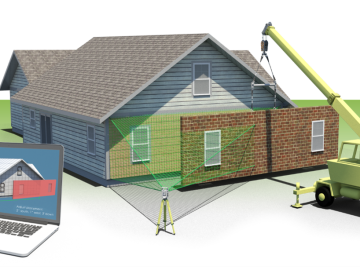
Researchers at ORNL have developed a tool that provides accurate measurements and positioning directions to those installing energy-efficient panels over existing building exteriors. This method will decrease installation time and cost by more than 25%.
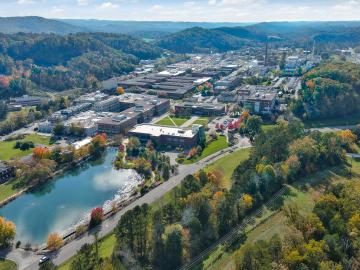
Several significant science and energy projects led by the ORNL will receive a total of $497 million in funding from the Inflation Reduction Act.

Materials scientist Denise Antunes da Silva researches ways to reduce concrete’s embodied carbon in the Sustainable Building Materials Laboratory at ORNL, a research space dedicated to studying environmentally friendly building materials. Credit: ORNL, U.S. Dept. of Energy
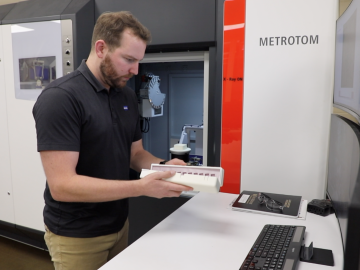
A new deep-learning framework developed at ORNL is speeding up the process of inspecting additively manufactured metal parts using X-ray computed tomography, or CT, while increasing the accuracy of the results. The reduced costs for time, labor, maintenance and energy are expected to accelerate expansion of additive manufacturing, or 3D printing.