
Filter News
Area of Research
- Advanced Manufacturing (22)
- Biology and Environment (21)
- Building Technologies (1)
- Clean Energy (88)
- Computational Biology (1)
- Fusion and Fission (4)
- Fusion Energy (1)
- Isotopes (1)
- Materials (26)
- Materials for Computing (7)
- National Security (14)
- Neutron Science (15)
- Nuclear Science and Technology (5)
- Sensors and Controls (1)
- Supercomputing (21)
News Topics
- (-) 3-D Printing/Advanced Manufacturing (124)
- (-) Coronavirus (46)
- (-) Security (24)
- (-) Transformational Challenge Reactor (7)
- Advanced Reactors (34)
- Artificial Intelligence (94)
- Big Data (57)
- Bioenergy (92)
- Biology (100)
- Biomedical (59)
- Biotechnology (22)
- Buildings (57)
- Chemical Sciences (66)
- Clean Water (30)
- Climate Change (101)
- Composites (28)
- Computer Science (192)
- Critical Materials (27)
- Cybersecurity (35)
- Decarbonization (80)
- Education (4)
- Element Discovery (1)
- Emergency (2)
- Energy Storage (109)
- Environment (196)
- Exascale Computing (38)
- Fossil Energy (6)
- Frontier (43)
- Fusion (55)
- Grid (65)
- High-Performance Computing (87)
- Hydropower (11)
- Irradiation (3)
- Isotopes (53)
- ITER (7)
- Machine Learning (48)
- Materials (144)
- Materials Science (141)
- Mathematics (9)
- Mercury (12)
- Microelectronics (3)
- Microscopy (51)
- Molten Salt (8)
- Nanotechnology (60)
- National Security (65)
- Net Zero (14)
- Neutron Science (131)
- Nuclear Energy (109)
- Partnerships (46)
- Physics (62)
- Polymers (33)
- Quantum Computing (35)
- Quantum Science (69)
- Renewable Energy (2)
- Simulation (49)
- Software (1)
- Space Exploration (25)
- Statistics (3)
- Summit (58)
- Sustainable Energy (129)
- Transportation (97)
Media Contacts

Brittany Rodriguez never imagined she would pursue a science career at a Department of Energy national laboratory. However, after some encouraging words from her mother, input from key mentors at the University of Texas Rio Grande Valley, or UTRGV, and a lot of hard work, Rodriguez landed at DOE’s Manufacturing Demonstration Facility, or MDF, at Oak Ridge National Laboratory.
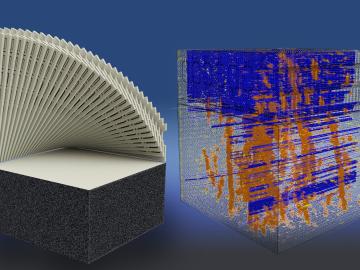
The Department of Energy’s Oak Ridge National Laboratory has publicly released a new set of additive manufacturing data that industry and researchers can use to evaluate and improve the quality of 3D-printed components. The breadth of the datasets can significantly boost efforts to verify the quality of additively manufactured parts using only information gathered during printing, without requiring expensive and time-consuming post-production analysis.
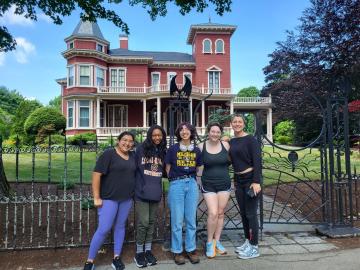
Participants in the SM2ART Research Experience for Undergraduates program got the chance to see what life is like in a research setting. REU participant Brianna Greer studied banana fibers as a reinforcing material in making lightweight parts for cars and bicycles.

Advanced materials research to enable energy-efficient, cost-competitive and environmentally friendly technologies for the United States and Japan is the goal of a memorandum of understanding, or MOU, between the Department of Energy’s Oak Ridge National Laboratory and Japan’s National Institute of Materials Science.

Researchers at ORNL have developed the first additive manufacturing slicing computer application to simultaneously speed and simplify digital conversion of accurate, large-format three-dimensional parts in a factory production setting.

Oak Ridge National Laboratory scientists ingeniously created a sustainable, soft material by combining rubber with woody reinforcements and incorporating “smart” linkages between the components that unlock on demand.
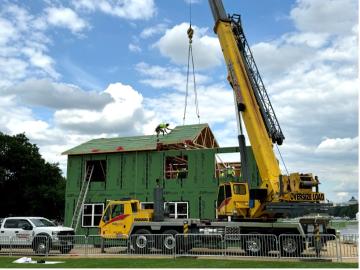
Building innovations from ORNL will be on display in Washington, D.C. on the National Mall June 7 to June 9, 2024, during the U.S. Department of Housing and Urban Development’s Innovation Housing Showcase. For the first time, ORNL’s real-time building evaluator was demonstrated outside of a laboratory setting and deployed for building construction.
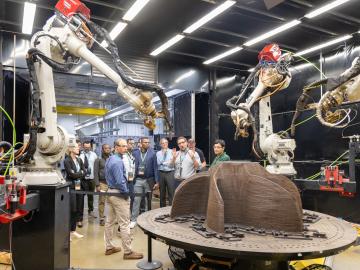
Momentum for manufacturing innovation in the United States got a boost during the inaugural MDF Innovation Days, held recently at the U.S. Department of Energy Manufacturing Demonstration Facility at Oak Ridge National Laboratory.

Mohamad Zineddin hopes to establish an interdisciplinary center of excellence for nuclear security at ORNL, combining critical infrastructure assessment and protection, risk mitigation, leadership in nuclear security, education and training, nuclear security culture and resilience strategies and techniques.
Simulations performed on the Summit supercomputer at ORNL are cutting through that time and expense by helping researchers digitally customize the ideal alloy.