
Filter News
Area of Research
News Topics
- (-) Composites (28)
- (-) Critical Materials (28)
- (-) Mercury (12)
- (-) Molten Salt (8)
- 3-D Printing/Advanced Manufacturing (125)
- Advanced Reactors (34)
- Artificial Intelligence (94)
- Big Data (58)
- Bioenergy (92)
- Biology (100)
- Biomedical (59)
- Biotechnology (22)
- Buildings (57)
- Chemical Sciences (66)
- Clean Water (30)
- Climate Change (101)
- Computer Science (193)
- Coronavirus (46)
- Cybersecurity (35)
- Decarbonization (80)
- Education (4)
- Element Discovery (1)
- Emergency (2)
- Energy Storage (109)
- Environment (196)
- Exascale Computing (39)
- Fossil Energy (6)
- Frontier (44)
- Fusion (55)
- Grid (65)
- High-Performance Computing (88)
- Hydropower (11)
- Irradiation (3)
- Isotopes (53)
- ITER (7)
- Machine Learning (48)
- Materials (144)
- Materials Science (142)
- Mathematics (9)
- Microelectronics (3)
- Microscopy (51)
- Nanotechnology (60)
- National Security (65)
- Net Zero (14)
- Neutron Science (131)
- Nuclear Energy (109)
- Partnerships (46)
- Physics (62)
- Polymers (33)
- Quantum Computing (35)
- Quantum Science (69)
- Renewable Energy (2)
- Security (24)
- Simulation (49)
- Software (1)
- Space Exploration (25)
- Statistics (3)
- Summit (59)
- Sustainable Energy (129)
- Transformational Challenge Reactor (7)
- Transportation (97)
Media Contacts

The world’s fastest supercomputer helped researchers simulate synthesizing a material harder and tougher than a diamond — or any other substance on Earth. The study used Frontier to predict the likeliest strategy to synthesize such a material, thought to exist so far only within the interiors of giant exoplanets, or planets beyond our solar system.

Two ORNL teams recently completed Cohort 18 of Energy I-Corps, an immersive two-month training program where the scientists define their technology’s value propositions, conduct stakeholder discovery interviews and develop viable market pathways.

Brian Sanders is focused on impactful, multidisciplinary science at Oak Ridge National Laboratory, developing solutions for everything from improved imaging of plant-microbe interactions that influence ecosystem health to advancing new treatments for cancer and viral infections.

Brittany Rodriguez never imagined she would pursue a science career at a Department of Energy national laboratory. However, after some encouraging words from her mother, input from key mentors at the University of Texas Rio Grande Valley, or UTRGV, and a lot of hard work, Rodriguez landed at DOE’s Manufacturing Demonstration Facility, or MDF, at Oak Ridge National Laboratory.

Advanced materials research to enable energy-efficient, cost-competitive and environmentally friendly technologies for the United States and Japan is the goal of a memorandum of understanding, or MOU, between the Department of Energy’s Oak Ridge National Laboratory and Japan’s National Institute of Materials Science.

Researchers at ORNL and the University of Maine have designed and 3D-printed a single-piece, recyclable natural-material floor panel tested to be strong enough to replace construction materials like steel.

ORNL researchers used electron-beam additive manufacturing to 3D-print the first complex, defect-free tungsten parts with complex geometries.

A collection of seven technologies for lithium recovery developed by scientists from ORNL has been licensed to Element3, a Texas-based company focused on extracting lithium from wastewater produced by oil and gas production.
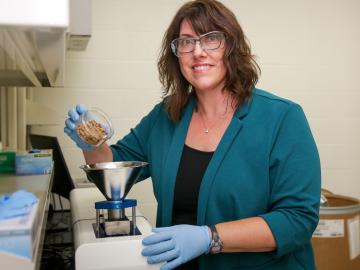
ORNL’s Erin Webb is co-leading a new Circular Bioeconomy Systems Convergent Research Initiative focused on advancing production and use of renewable carbon from Tennessee to meet societal needs.

In a win for chemistry, inventors at ORNL have designed a closed-loop path for synthesizing an exceptionally tough carbon-fiber-reinforced polymer, or CFRP, and later recovering all of its starting materials.