
Filter News
Area of Research
News Topics
- (-) 3-D Printing/Advanced Manufacturing (15)
- (-) Transportation (12)
- Advanced Reactors (7)
- Artificial Intelligence (12)
- Big Data (7)
- Bioenergy (9)
- Biomedical (5)
- Biotechnology (1)
- Clean Water (5)
- Composites (2)
- Computer Science (35)
- Cybersecurity (5)
- Energy Storage (8)
- Environment (19)
- Exascale Computing (2)
- Frontier (2)
- Fusion (5)
- Grid (5)
- Isotopes (1)
- Machine Learning (5)
- Materials Science (20)
- Mercury (1)
- Microscopy (5)
- Molten Salt (1)
- Nanotechnology (6)
- Neutron Science (18)
- Nuclear Energy (17)
- Physics (6)
- Polymers (2)
- Quantum Science (10)
- Security (2)
- Space Exploration (4)
- Summit (9)
- Sustainable Energy (8)
Media Contacts

Using additive manufacturing, scientists experimenting with tungsten at Oak Ridge National Laboratory hope to unlock new potential of the high-performance heat-transferring material used to protect components from the plasma inside a fusion reactor. Fusion requires hydrogen isotopes to reach millions of degrees.
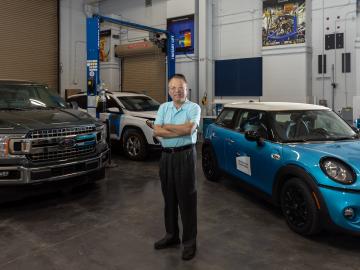
In Hong Wang’s world, nothing is beyond control. Before joining Oak Ridge National Laboratory as a senior distinguished researcher in transportation systems, he spent more than three decades studying the control of complex industrial systems in the United Kingdom.
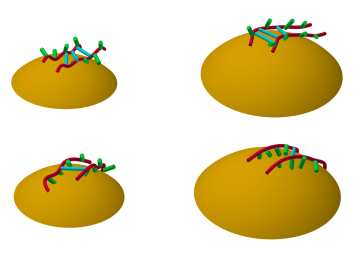
A team of researchers at Oak Ridge National Laboratory have demonstrated that designed synthetic polymers can serve as a high-performance binding material for next-generation lithium-ion batteries.
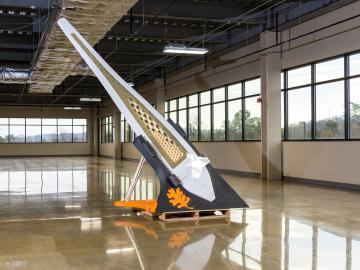
In the shifting landscape of global manufacturing, American ingenuity is once again giving U.S companies an edge with radical productivity improvements as a result of advanced materials and robotic systems developed at the Department of Energy’s Manufacturing Demonstration Facility (MDF) at Oak Ridge National Laboratory.
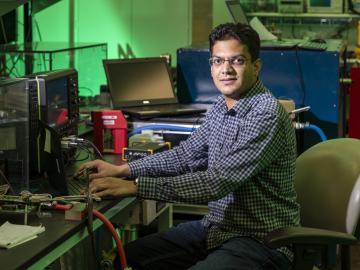
Galigekere is principal investigator for the breakthrough work in fast, wireless charging of electric vehicles being performed at the National Transportation Research Center at Oak Ridge National Laboratory.

OAK RIDGE, Tenn., May 8, 2019—Oak Ridge National Laboratory and Lincoln Electric (NASDAQ: LECO) announced their continued collaboration on large-scale, robotic additive manufacturing technology at the Department of Energy’s Advanced Manufacturing InnovationXLab Summit.
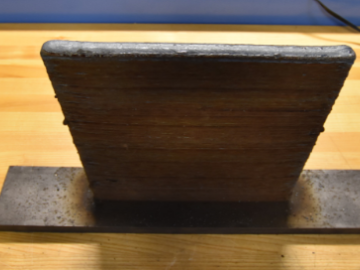
A novel additive manufacturing method developed by researchers at Oak Ridge National Laboratory could be a promising alternative for low-cost, high-quality production of large-scale metal parts with less material waste.
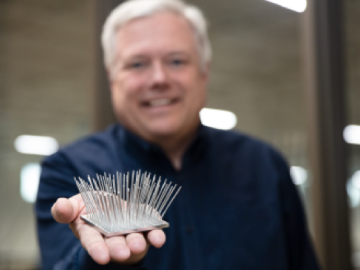
When Scott Smith looks at a machine tool, he thinks not about what the powerful equipment used to shape metal can do – he’s imagining what it could do with the right added parts and strategies. As ORNL’s leader for a newly formed group, Machining and Machine Tool Research, Smith will have the opportunity to do just that.
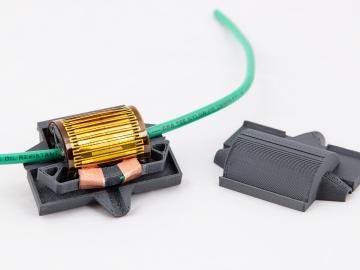
Scientists at Oak Ridge National Laboratory have developed a low-cost, printed, flexible sensor that can wrap around power cables to precisely monitor electrical loads from household appliances to support grid operations.
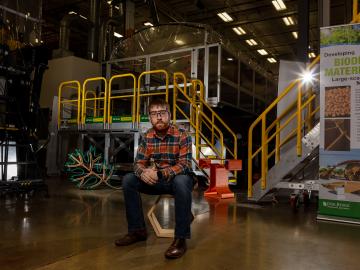
Alex Roschli is no stranger to finding himself in unique situations. After all, the early career researcher in ORNL’s Manufacturing Systems Research group bears a last name that only 29 other people share in the United States, and he’s certain he’s the only Roschli (a moniker that hails from Switzerland) with the first name Alex.