Filter News
Area of Research
- (-) Advanced Manufacturing (9)
- (-) Neutron Science (30)
- Biology and Environment (89)
- Biology and Soft Matter (1)
- Building Technologies (3)
- Clean Energy (118)
- Computational Biology (2)
- Computational Engineering (2)
- Computer Science (5)
- Electricity and Smart Grid (2)
- Functional Materials for Energy (2)
- Fusion and Fission (29)
- Fusion Energy (1)
- Isotopes (15)
- Materials (58)
- Materials for Computing (24)
- Mathematics (1)
- National Security (32)
- Nuclear Science and Technology (1)
- Quantum information Science (3)
- Renewable Energy (1)
- Sensors and Controls (1)
- Supercomputing (60)
- Transportation Systems (1)
News Topics
- 3-D Printing/Advanced Manufacturing (7)
- Artificial Intelligence (4)
- Biology (4)
- Biomedical (2)
- Chemical Sciences (1)
- Composites (2)
- Computer Science (5)
- Coronavirus (2)
- Cybersecurity (1)
- Decarbonization (1)
- Energy Storage (2)
- Environment (1)
- Frontier (1)
- Fusion (1)
- High-Performance Computing (1)
- Materials (10)
- Materials Science (8)
- Microscopy (1)
- Nanotechnology (2)
- National Security (1)
- Neutron Science (24)
- Physics (2)
- Quantum Computing (1)
- Quantum Science (3)
- Security (1)
- Space Exploration (3)
- Summit (1)
- Sustainable Energy (4)
- Transportation (1)
Media Contacts

Oak Ridge National Laboratory researchers combined additive manufacturing with conventional compression molding to produce high-performance thermoplastic composites reinforced with short carbon fibers.
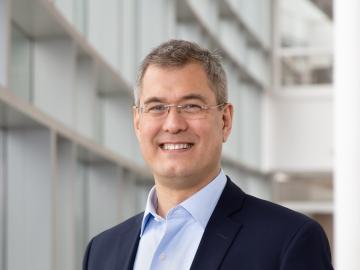
Ken Andersen has been named associate laboratory director for the Neutron Sciences Directorate, or NScD, at the Department of Energy’s Oak Ridge National Laboratory.
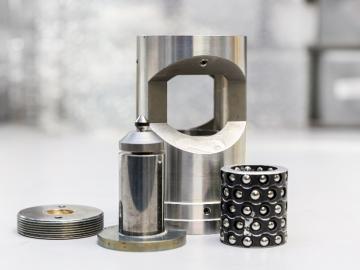
Researchers at Oak Ridge National Laboratory’s Spallation Neutron Source have developed a diamond anvil pressure cell that will enable high-pressure science currently not possible at any other neutron source in the world.

A team of Oak Ridge National Laboratory researchers demonstrated that an additively manufactured hot stamping die – a tool used to create car body components – cooled faster than those produced by conventional manufacturing methods.
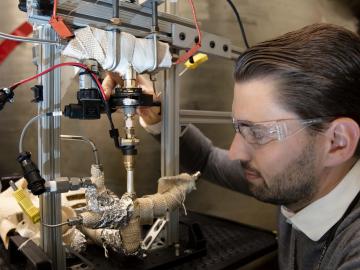
For a researcher who started out in mechanical engineering with a focus on engine combustion, Martin Wissink has learned a lot about neutrons on the job

Oak Ridge National Laboratory researchers have demonstrated that a new class of superalloys made of cobalt and nickel remains crack-free and defect-resistant in extreme heat, making them conducive for use in metal-based 3D printing applications.
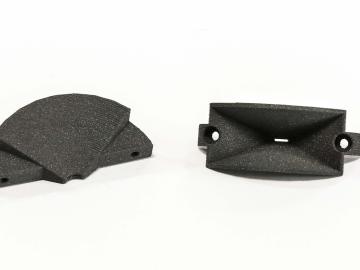
The ExOne Company, the global leader in industrial sand and metal 3D printers using binder jetting technology, announced it has reached a commercial license agreement with Oak Ridge National Laboratory to 3D print parts in aluminum-infiltrated boron carbide.
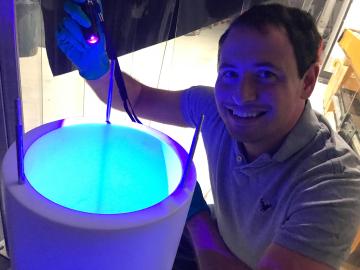
The COHERENT particle physics experiment at the Department of Energy’s Oak Ridge National Laboratory has firmly established the existence of a new kind of neutrino interaction.