Filter News
Area of Research
News Type
News Topics
- (-) Composites (3)
- (-) Materials Science (13)
- 3-D Printing/Advanced Manufacturing (16)
- Advanced Reactors (2)
- Artificial Intelligence (5)
- Big Data (3)
- Bioenergy (12)
- Biology (18)
- Biomedical (6)
- Biotechnology (4)
- Buildings (6)
- Chemical Sciences (3)
- Clean Water (8)
- Climate Change (10)
- Computer Science (21)
- Coronavirus (5)
- Critical Materials (2)
- Cybersecurity (2)
- Decarbonization (4)
- Energy Storage (10)
- Environment (34)
- Exascale Computing (2)
- Frontier (1)
- Fusion (3)
- Grid (6)
- High-Performance Computing (14)
- Isotopes (8)
- ITER (3)
- Materials (21)
- Mathematics (1)
- Mercury (3)
- Microscopy (6)
- Nanotechnology (5)
- National Security (4)
- Net Zero (1)
- Neutron Science (10)
- Nuclear Energy (4)
- Physics (2)
- Polymers (2)
- Quantum Computing (2)
- Quantum Science (7)
- Security (2)
- Space Exploration (4)
- Statistics (1)
- Summit (4)
- Sustainable Energy (27)
- Transportation (14)
Media Contacts

Energy Secretary Jennifer Granholm visited ORNL on Nov. 22 for a two-hour tour, meeting top scientists and engineers as they highlighted projects and world-leading capabilities that address some of the country’s most complex research and technical challenges.

A team led by the U.S. Department of Energy’s Oak Ridge National Laboratory demonstrated the viability of a “quantum entanglement witness” capable of proving the presence of entanglement between magnetic particles, or spins, in a quantum material.

A multidisciplinary team of scientists at ORNL has applied a laser-interference structuring, or LIS, technique that makes significant strides toward eliminating the need for hazardous chemicals in corrosion protection for vehicles.

A research team at Oak Ridge National Laboratory have 3D printed a thermal protection shield, or TPS, for a capsule that will launch with the Cygnus cargo spacecraft as part of the supply mission to the International Space Station.

Oak Ridge National Laboratory researchers have developed a new catalyst for converting ethanol into C3+ olefins – the chemical

Scientists at Oak Ridge National Laboratory have developed a solvent that results in a more environmentally friendly process to recover valuable materials from used lithium-ion batteries, supports a stable domestic supply chain for new batteries
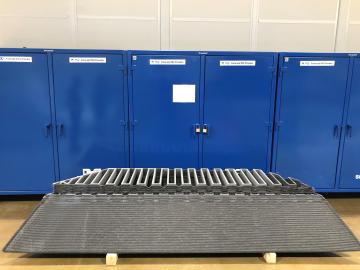
Oak Ridge National Laboratory researchers, in collaboration with Cincinnati Inc., demonstrated the potential for using multimaterials and recycled composites in large-scale applications by 3D printing a mold that replicated a single facet of a

At the Department of Energy’s Oak Ridge National Laboratory, scientists use artificial intelligence, or AI, to accelerate the discovery and development of materials for energy and information technologies.

When COVID-19 was declared a pandemic in March 2020, Oak Ridge National Laboratory’s Parans Paranthaman suddenly found himself working from home like millions of others.

Oak Ridge National Laboratory researchers combined additive manufacturing with conventional compression molding to produce high-performance thermoplastic composites reinforced with short carbon fibers.