
Filter News
Area of Research
News Topics
- (-) 3-D Printing/Advanced Manufacturing (26)
- (-) Big Data (5)
- (-) Materials (32)
- Advanced Reactors (2)
- Artificial Intelligence (7)
- Bioenergy (13)
- Biology (23)
- Biomedical (10)
- Biotechnology (5)
- Buildings (13)
- Chemical Sciences (7)
- Clean Water (8)
- Climate Change (11)
- Composites (6)
- Computer Science (30)
- Coronavirus (10)
- Critical Materials (4)
- Cybersecurity (5)
- Decarbonization (7)
- Energy Storage (22)
- Environment (39)
- Exascale Computing (2)
- Frontier (4)
- Fusion (8)
- Grid (11)
- High-Performance Computing (19)
- Isotopes (12)
- ITER (4)
- Machine Learning (1)
- Materials Science (22)
- Mathematics (1)
- Mercury (3)
- Microscopy (10)
- Nanotechnology (10)
- National Security (7)
- Net Zero (1)
- Neutron Science (18)
- Nuclear Energy (6)
- Physics (3)
- Polymers (5)
- Quantum Computing (5)
- Quantum Science (12)
- Security (3)
- Space Exploration (4)
- Statistics (1)
- Summit (9)
- Sustainable Energy (35)
- Transportation (21)
Media Contacts
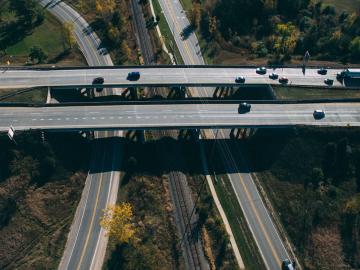
Through a consortium of Department of Energy national laboratories, ORNL scientists are applying their expertise to provide solutions that enable the commercialization of emission-free hydrogen fuel cell technology for heavy-duty
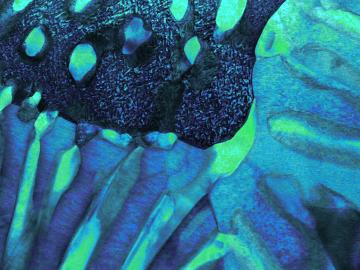
Oak Ridge National Laboratory scientists proved molybdenum titanium carbide, a refractory metal alloy that can withstand extreme temperature environments, can also be crack free and dense when produced with electron beam powder bed fusion.
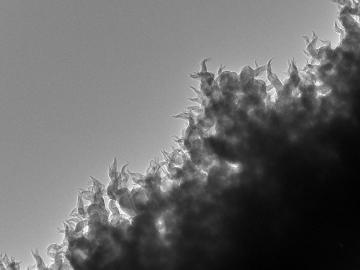
In a new twist to an existing award-winning ORNL technology, researchers have developed an electrocatalyst that enables water and carbon dioxide to be split and the atoms recombined to form higher weight hydrocarbons for gasoline, diesel and jet fuel.
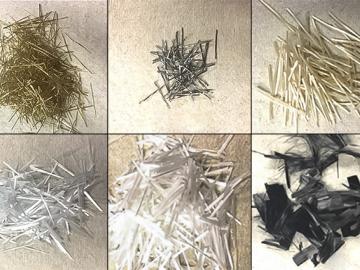
A team of researchers at Oak Ridge National Laboratory and the University of Tennessee have developed a concrete mix that demonstrated high early strength within six hours of mixing, potentially doubling the production capacity for the precast industry.

Oak Ridge National Laboratory researchers combined additive manufacturing with conventional compression molding to produce high-performance thermoplastic composites reinforced with short carbon fibers.
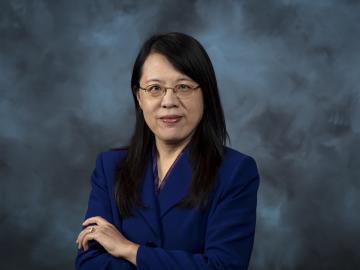
Xin Sun has been selected as the associate laboratory director for the Energy Science and Technology Directorate, or ESTD, at the Department of Energy’s Oak Ridge National Laboratory.

A team of Oak Ridge National Laboratory researchers demonstrated that an additively manufactured hot stamping die – a tool used to create car body components – cooled faster than those produced by conventional manufacturing methods.

Twenty-seven ORNL researchers Zoomed into 11 middle schools across Tennessee during the annual Engineers Week in February. East Tennessee schools throughout Oak Ridge and Roane, Sevier, Blount and Loudon counties participated, with three West Tennessee schools joining in.
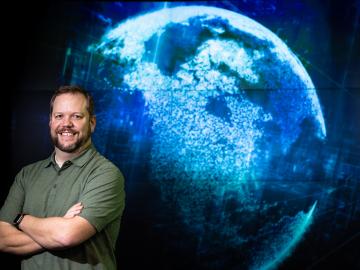
Cory Stuart of ORNL applies his expertise as a systems engineer to ensure the secure and timely transfer of millions of measurements of Earth’s atmosphere, fueling science around the world.

Oak Ridge National Laboratory researchers have demonstrated that a new class of superalloys made of cobalt and nickel remains crack-free and defect-resistant in extreme heat, making them conducive for use in metal-based 3D printing applications.