Filter News
Area of Research
News Type
News Topics
- (-) 3-D Printing/Advanced Manufacturing (66)
- (-) Critical Materials (13)
- Advanced Reactors (21)
- Artificial Intelligence (58)
- Big Data (36)
- Bioenergy (64)
- Biology (74)
- Biomedical (39)
- Biotechnology (13)
- Buildings (35)
- Chemical Sciences (29)
- Clean Water (27)
- Climate Change (68)
- Composites (15)
- Computer Science (119)
- Coronavirus (28)
- Cybersecurity (17)
- Decarbonization (51)
- Education (1)
- Emergency (2)
- Energy Storage (59)
- Environment (143)
- Exascale Computing (25)
- Fossil Energy (4)
- Frontier (24)
- Fusion (37)
- Grid (43)
- High-Performance Computing (53)
- Hydropower (11)
- Irradiation (2)
- Isotopes (30)
- ITER (5)
- Machine Learning (31)
- Materials (75)
- Materials Science (75)
- Mathematics (6)
- Mercury (10)
- Microelectronics (2)
- Microscopy (31)
- Molten Salt (6)
- Nanotechnology (28)
- National Security (36)
- Net Zero (9)
- Neutron Science (73)
- Nuclear Energy (70)
- Partnerships (15)
- Physics (30)
- Polymers (17)
- Quantum Computing (22)
- Quantum Science (38)
- Renewable Energy (1)
- Security (11)
- Simulation (35)
- Software (1)
- Space Exploration (22)
- Statistics (1)
- Summit (36)
- Sustainable Energy (87)
- Transformational Challenge Reactor (3)
- Transportation (62)
Media Contacts

Oak Ridge National Laboratory scientists ingeniously created a sustainable, soft material by combining rubber with woody reinforcements and incorporating “smart” linkages between the components that unlock on demand.
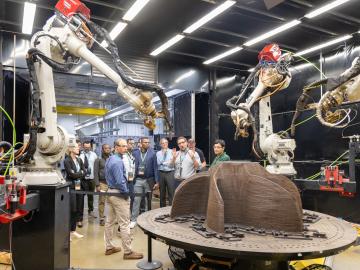
Momentum for manufacturing innovation in the United States got a boost during the inaugural MDF Innovation Days, held recently at the U.S. Department of Energy Manufacturing Demonstration Facility at Oak Ridge National Laboratory.

ORNL researchers used electron-beam additive manufacturing to 3D-print the first complex, defect-free tungsten parts with complex geometries.
Simulations performed on the Summit supercomputer at ORNL are cutting through that time and expense by helping researchers digitally customize the ideal alloy.
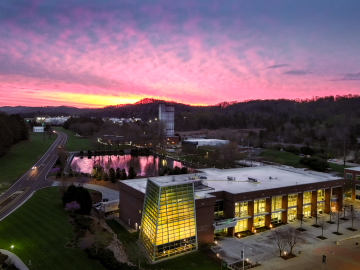
Rishi Pillai and his research team from ORNL will receive a Best Paper award from the American Society of Mechanical Engineers International Gas Turbine Institute in June at the Turbo Expo 2024 in London.
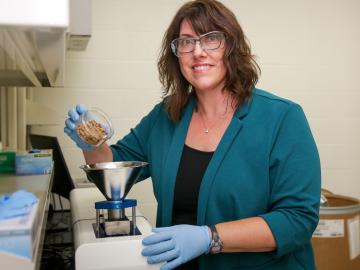
ORNL’s Erin Webb is co-leading a new Circular Bioeconomy Systems Convergent Research Initiative focused on advancing production and use of renewable carbon from Tennessee to meet societal needs.

Scientists at ORNL have developed 3D-printed collimator techniques that can be used to custom design collimators that better filter out noise during different types of neutron scattering experiments
ORNL scientists have determined how to avoid costly and potentially irreparable damage to large metallic parts fabricated through additive manufacturing, also known as 3D printing, that is caused by residual stress in the material.
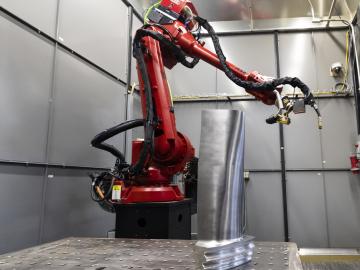
Researchers at ORNL became the first to 3D-print large rotating steam turbine blades for generating energy in power plants.

Nuclear engineering students from the United States Military Academy and United States Naval Academy are working with researchers at ORNL to complete design concepts for a nuclear propulsion rocket to go to space in 2027 as part of the Defense Advanced Research Projects Agency DRACO program.