
Filter News
Area of Research
- Advanced Manufacturing (14)
- Biology and Environment (37)
- Biology and Soft Matter (1)
- Building Technologies (1)
- Clean Energy (72)
- Computational Engineering (2)
- Computer Science (4)
- Fusion and Fission (29)
- Fusion Energy (13)
- Isotopes (2)
- Materials (25)
- Materials for Computing (3)
- Mathematics (1)
- National Security (13)
- Neutron Science (9)
- Nuclear Science and Technology (28)
- Nuclear Systems Modeling, Simulation and Validation (1)
- Supercomputing (16)
- Transportation Systems (1)
News Type
News Topics
- (-) 3-D Printing/Advanced Manufacturing (70)
- (-) Clean Water (27)
- (-) Decarbonization (55)
- (-) Fusion (40)
- (-) Machine Learning (33)
- (-) Molten Salt (6)
- (-) Nuclear Energy (74)
- Advanced Reactors (21)
- Artificial Intelligence (59)
- Big Data (41)
- Bioenergy (67)
- Biology (77)
- Biomedical (39)
- Biotechnology (14)
- Buildings (38)
- Chemical Sciences (34)
- Climate Change (72)
- Composites (15)
- Computer Science (123)
- Coronavirus (28)
- Critical Materials (14)
- Cybersecurity (17)
- Education (1)
- Emergency (2)
- Energy Storage (60)
- Environment (147)
- Exascale Computing (26)
- Fossil Energy (5)
- Frontier (25)
- Grid (44)
- High-Performance Computing (55)
- Hydropower (11)
- Irradiation (2)
- Isotopes (32)
- ITER (5)
- Materials (78)
- Materials Science (79)
- Mathematics (9)
- Mercury (10)
- Microelectronics (2)
- Microscopy (31)
- Nanotechnology (28)
- National Security (40)
- Net Zero (10)
- Neutron Science (74)
- Partnerships (17)
- Physics (32)
- Polymers (17)
- Quantum Computing (24)
- Quantum Science (40)
- Renewable Energy (1)
- Security (12)
- Simulation (38)
- Software (1)
- Space Exploration (22)
- Statistics (2)
- Summit (36)
- Sustainable Energy (89)
- Transformational Challenge Reactor (3)
- Transportation (62)
Media Contacts

Equipment and expertise from Oak Ridge National Laboratory will allow scientists studying fusion energy and technologies to acquire crucial data during landmark fusion experiments in Europe.
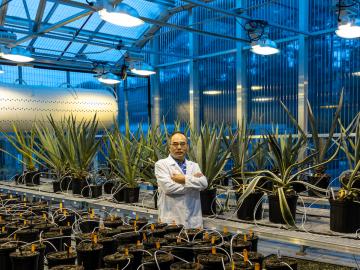
Scientists at ORNL have discovered a single gene that simultaneously boosts plant growth and tolerance for stresses such as drought and salt, all while tackling the root cause of climate change by enabling plants to pull more carbon dioxide from the atmosphere.
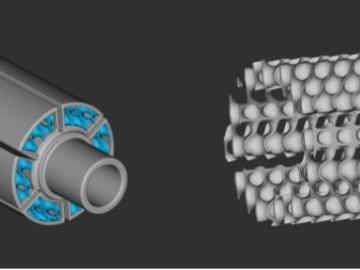
Additive manufacturing can make the design and production of specialized tools for geothermal energy cheaper and more efficient, according to a study by Oak Ridge National Laboratory.

Oak Ridge National Laboratory expertise in fission and fusion has come together to form a new collaboration, the Fusion Energy Reactor Models Integrator, or FERMI
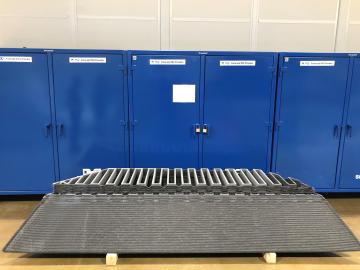
Oak Ridge National Laboratory researchers, in collaboration with Cincinnati Inc., demonstrated the potential for using multimaterials and recycled composites in large-scale applications by 3D printing a mold that replicated a single facet of a
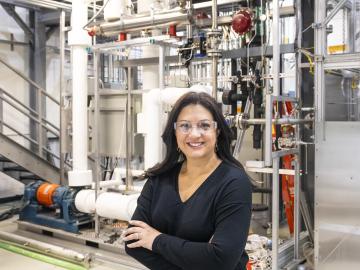
Toward the goal of bringing the next generation of nuclear power reactor technology online this decade, ORNL and Analysis and Measurement Services Corporation have successfully completed loop testing of instrument and control sensors for an advanced reactor design for small modular reactors.
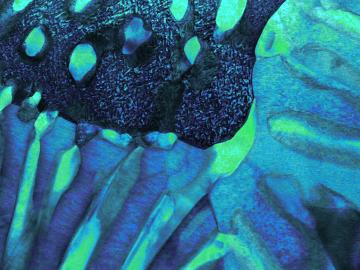
Oak Ridge National Laboratory scientists proved molybdenum titanium carbide, a refractory metal alloy that can withstand extreme temperature environments, can also be crack free and dense when produced with electron beam powder bed fusion.

Researchers at Oak Ridge National Laboratory have identified a statistical relationship between the growth of cities and the spread of paved surfaces like roads and sidewalks. These impervious surfaces impede the flow of water into the ground, affecting the water cycle and, by extension, the climate.

Oak Ridge National Laboratory researchers combined additive manufacturing with conventional compression molding to produce high-performance thermoplastic composites reinforced with short carbon fibers.

A team of Oak Ridge National Laboratory researchers demonstrated that an additively manufactured hot stamping die – a tool used to create car body components – cooled faster than those produced by conventional manufacturing methods.