
Filter News
Area of Research
News Topics
- (-) 3-D Printing/Advanced Manufacturing (41)
- (-) ITER (2)
- Advanced Reactors (8)
- Artificial Intelligence (48)
- Big Data (26)
- Bioenergy (51)
- Biology (60)
- Biomedical (29)
- Biotechnology (11)
- Buildings (19)
- Chemical Sciences (25)
- Clean Water (14)
- Climate Change (50)
- Composites (8)
- Computer Science (86)
- Coronavirus (17)
- Critical Materials (3)
- Cybersecurity (14)
- Decarbonization (46)
- Education (1)
- Emergency (2)
- Energy Storage (29)
- Environment (104)
- Exascale Computing (26)
- Fossil Energy (4)
- Frontier (24)
- Fusion (31)
- Grid (25)
- High-Performance Computing (44)
- Hydropower (5)
- Isotopes (27)
- Machine Learning (22)
- Materials (43)
- Materials Science (45)
- Mathematics (7)
- Mercury (7)
- Microelectronics (2)
- Microscopy (20)
- Molten Salt (1)
- Nanotechnology (16)
- National Security (39)
- Net Zero (8)
- Neutron Science (47)
- Nuclear Energy (55)
- Partnerships (18)
- Physics (29)
- Polymers (8)
- Quantum Computing (21)
- Quantum Science (30)
- Renewable Energy (1)
- Security (11)
- Simulation (32)
- Software (1)
- Space Exploration (12)
- Statistics (1)
- Summit (30)
- Sustainable Energy (47)
- Transformational Challenge Reactor (3)
- Transportation (27)
Media Contacts

Scientists at ORNL have developed 3-D-printed collimator techniques that can be used to custom design collimators that better filter out noise during different types of neutron scattering experiments
ORNL scientists have determined how to avoid costly and potentially irreparable damage to large metallic parts fabricated through additive manufacturing, also known as 3D printing, that is caused by residual stress in the material.
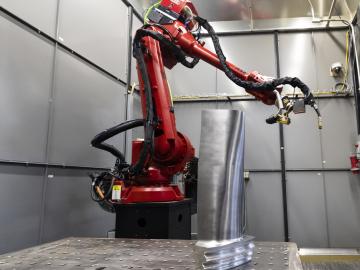
Researchers at ORNL became the first to 3D-print large rotating steam turbine blades for generating energy in power plants.

Researchers at the Department of Energy’s Oak Ridge National Laboratory, in collaboration with NASA, are taking additive manufacturing to the final frontier by 3D printing the same kind of wheel as the design used by NASA for its robotic lunar rover, demonstrating the technology for specialized parts needed for space exploration.

Yarom Polsky, director of the Manufacturing Science Division, or MSD, at the Department of Energy’s Oak Ridge National Laboratory, has been elected a Fellow of the American Society of Mechanical Engineers, or ASME.
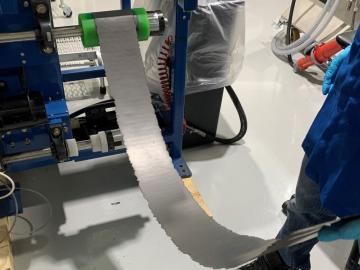
Early experiments at the Department of Energy’s Oak Ridge National Laboratory have revealed significant benefits to a dry battery manufacturing process. This eliminates the use of solvents and is more affordable, while showing promise for delivering a battery that is durable, less weighed down by inactive elements, and able to maintain a high capacity after use.
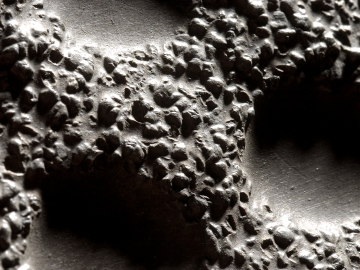
For more than 100 years, Magotteaux has provided grinding materials and castings for the mining, cement and aggregates industries. The company, based in Belgium, began its international expansion in 1968. Its second international plant has been a critical part of the Pulaski, Tennessee, economy since 1972.
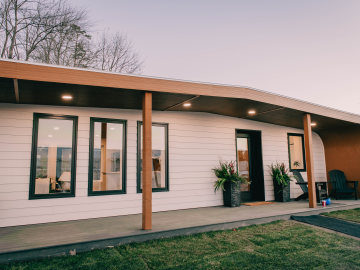
On the grounds of the University of Maine’s Advanced Structures and Composites Center sits the nation’s first additively manufactured home made entirely from biobased materials - BioHome3D.

How an Alvin M. Weinberg Fellow is increasing security for critical infrastructure components

To achieve practical energy from fusion, extreme heat from the fusion system “blanket” component must be extracted safely and efficiently. ORNL fusion experts are exploring how tiny 3D-printed obstacles placed inside the narrow pipes of a custom-made cooling system could be a solution for removing heat from the blanket.