
Filter News
Area of Research
- (-) Clean Energy (114)
- Advanced Manufacturing (15)
- Biology and Environment (31)
- Building Technologies (1)
- Computational Biology (1)
- Computational Engineering (2)
- Computer Science (8)
- Electricity and Smart Grid (2)
- Energy Sciences (1)
- Fusion and Fission (20)
- Fusion Energy (10)
- Isotopes (6)
- Materials (71)
- Materials for Computing (13)
- Mathematics (1)
- National Security (27)
- Neutron Science (59)
- Nuclear Science and Technology (27)
- Nuclear Systems Modeling, Simulation and Validation (1)
- Quantum information Science (7)
- Sensors and Controls (1)
- Supercomputing (56)
News Type
News Topics
- (-) 3-D Printing/Advanced Manufacturing (45)
- (-) Big Data (1)
- (-) Clean Water (7)
- (-) Cybersecurity (5)
- (-) Energy Storage (41)
- (-) Grid (28)
- (-) Machine Learning (2)
- (-) Materials (17)
- (-) Neutron Science (2)
- (-) Nuclear Energy (3)
- (-) Quantum Science (1)
- Advanced Reactors (2)
- Artificial Intelligence (3)
- Bioenergy (12)
- Biology (6)
- Biomedical (3)
- Biotechnology (2)
- Buildings (24)
- Chemical Sciences (4)
- Climate Change (14)
- Composites (11)
- Computer Science (16)
- Coronavirus (7)
- Critical Materials (4)
- Decarbonization (19)
- Environment (33)
- Fossil Energy (1)
- High-Performance Computing (3)
- Hydropower (2)
- Materials Science (13)
- Mathematics (2)
- Mercury (2)
- Microelectronics (1)
- Microscopy (4)
- Nanotechnology (3)
- National Security (1)
- Net Zero (2)
- Partnerships (4)
- Polymers (6)
- Security (3)
- Simulation (2)
- Space Exploration (3)
- Statistics (1)
- Summit (2)
- Sustainable Energy (41)
- Transportation (43)
Media Contacts
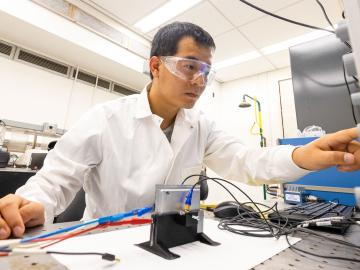
Scientists at Oak Ridge National Laboratory are using ultrasounds — usually associated with medical imaging — to check the health of an operating battery. The technique uses sensors as small as a thumbnail, which could be attached to a lithium-ion battery inside a car.
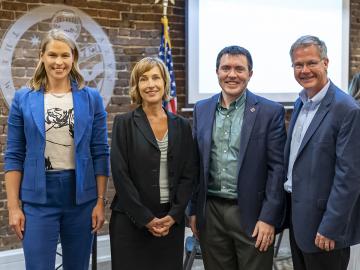
A crowd of investors and supporters turned out for last week’s Innovation Crossroads Showcase at the Knoxville Chamber as part of Innov865 Week. Sponsored by ORNL and the Tennessee Advanced Energy Business Council, the event celebrated deep-tech entrepreneurs and the Oak Ridge Corridor as a growing energy innovation hub for the nation.

To further the potential benefits of the nation’s hydropower resources, researchers at Oak Ridge National Laboratory have developed and maintain a comprehensive water energy digital platform called HydroSource.

Mechanical engineer Marm Dixit’s work is all about getting electricity to flow efficiently from one end of a solid-state battery to the other. It’s a high-stakes problem

When Andrew Sutton arrived at ORNL in late 2020, he knew the move would be significant in more ways than just a change in location.
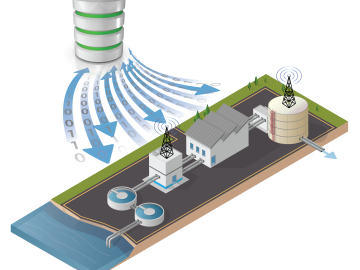
Oak Ridge National Laboratory scientists worked with the Colorado School of Mines and Baylor University to develop and test control methods for autonomous water treatment plants that use less energy and generate less waste.
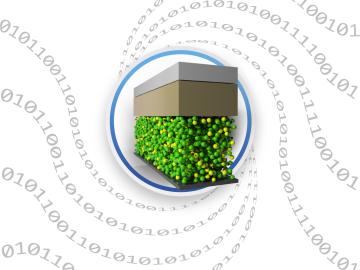
Scientists can speed the design of energy-dense solid-state batteries using a new tool created by Oak Ridge National Laboratory.

Burak Ozpineci started out at ORNL working on a novel project: introducing silicon carbide into power electronics for more efficient electric vehicles. Twenty years later, the car he drives contains those same components.

Oak Ridge National Laboratory researchers have developed a novel process to manufacture extreme heat resistant carbon-carbon composites. The performance of these materials will be tested in a U.S. Navy rocket that NASA will launch this fall.
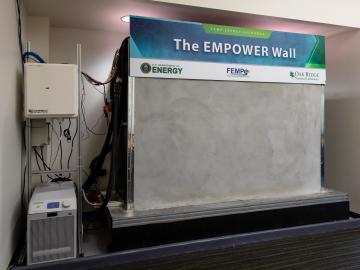
Oak Ridge National Laboratory researchers demonstrated that cooling cost savings could be achieved with a 3D printed concrete smart wall following a three-month field test.