
Filter News
Area of Research
- Advanced Manufacturing (14)
- Biology and Environment (47)
- Biology and Soft Matter (1)
- Building Technologies (1)
- Clean Energy (131)
- Climate and Environmental Systems (2)
- Computational Engineering (1)
- Computer Science (1)
- Energy Sciences (1)
- Fusion and Fission (7)
- Fusion Energy (2)
- Isotopes (20)
- Materials (40)
- Materials for Computing (6)
- Mathematics (1)
- National Security (19)
- Neutron Science (11)
- Nuclear Science and Technology (7)
- Quantum information Science (1)
- Supercomputing (40)
- Transportation Systems (2)
News Type
News Topics
- (-) 3-D Printing/Advanced Manufacturing (68)
- (-) Climate Change (70)
- (-) Cybersecurity (17)
- (-) Energy Storage (59)
- (-) Exascale Computing (26)
- (-) Frontier (25)
- (-) Isotopes (32)
- (-) Mercury (10)
- (-) Security (12)
- (-) Space Exploration (22)
- (-) Transportation (62)
- Advanced Reactors (21)
- Artificial Intelligence (59)
- Big Data (38)
- Bioenergy (65)
- Biology (75)
- Biomedical (39)
- Biotechnology (14)
- Buildings (37)
- Chemical Sciences (31)
- Clean Water (27)
- Composites (15)
- Computer Science (121)
- Coronavirus (28)
- Critical Materials (14)
- Decarbonization (53)
- Education (1)
- Emergency (2)
- Environment (144)
- Fossil Energy (4)
- Fusion (39)
- Grid (43)
- High-Performance Computing (54)
- Hydropower (11)
- Irradiation (2)
- ITER (5)
- Machine Learning (32)
- Materials (76)
- Materials Science (77)
- Mathematics (7)
- Microelectronics (2)
- Microscopy (31)
- Molten Salt (6)
- Nanotechnology (28)
- National Security (38)
- Net Zero (9)
- Neutron Science (74)
- Nuclear Energy (73)
- Partnerships (17)
- Physics (32)
- Polymers (17)
- Quantum Computing (24)
- Quantum Science (40)
- Renewable Energy (1)
- Simulation (37)
- Software (1)
- Statistics (1)
- Summit (36)
- Sustainable Energy (87)
- Transformational Challenge Reactor (3)
Media Contacts

In fiscal year 2023 — Oct. 1–Sept. 30, 2023 — Oak Ridge National Laboratory was awarded more than $8 million in technology maturation funding through the Department of Energy’s Technology Commercialization Fund, or TCF.

Currently, the biggest hurdle for electric vehicles, or EVs, is the development of advanced battery technology to extend driving range, safety and reliability.
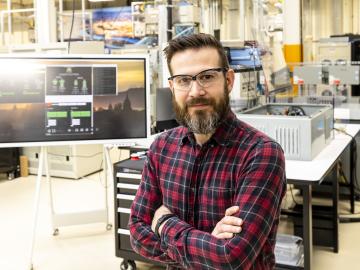
Steven Campbell can often be found deep among tall cases of power electronics, hunkered in his oversized blue lab coat, with 1500 volts of electricity flowing above his head. When interrupted in his laboratory at ORNL, Campbell will usually smile and duck his head.
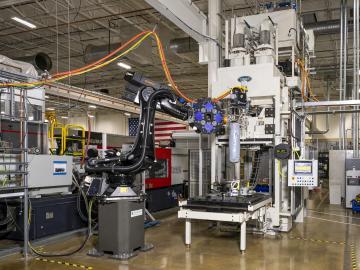
An Oak Ridge National Laboratory-developed advanced manufacturing technology, AMCM, was recently licensed by Orbital Composites and enables the rapid production of composite-based components, which could accelerate the decarbonization of vehicles

Researchers at the Department of Energy’s Oak Ridge National Laboratory, in collaboration with NASA, are taking additive manufacturing to the final frontier by 3D printing the same kind of wheel as the design used by NASA for its robotic lunar rover, demonstrating the technology for specialized parts needed for space exploration.
To better understand important dynamics at play in flood-prone coastal areas, Oak Ridge National Laboratory scientists working on simulations of Earth’s carbon and nutrient cycles paid a visit to experimentalists gathering data in a Texas wetland.
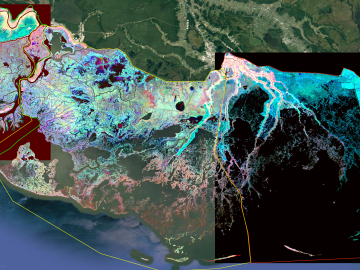
In 1993 as data managers at ORNL began compiling observations from field experiments for the National Aeronautics and Space Administration, the information fit on compact discs and was mailed to users along with printed manuals.
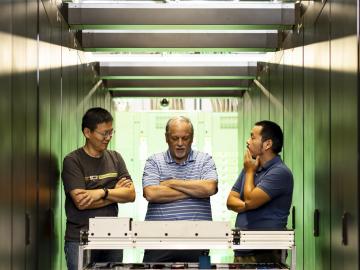
As Frontier, the world’s first exascale supercomputer, was being assembled at the Oak Ridge Leadership Computing Facility in 2021, understanding its performance on mixed-precision calculations remained a difficult prospect.
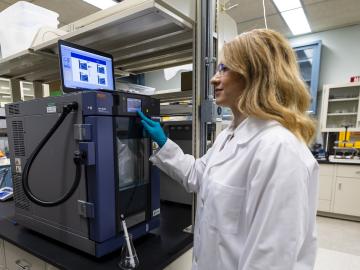
The common sounds in the background of daily life – like a refrigerator’s hum, an air conditioner’s whoosh and a heat pump’s buzz – often go unnoticed. These noises, however, are the heartbeat of a healthy building and integral for comfort and convenience.
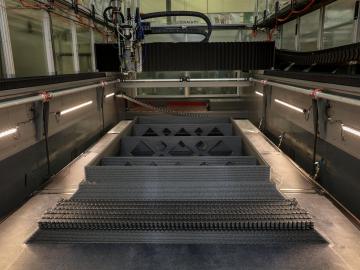
Oak Ridge National Laboratory researchers have conducted a comprehensive life cycle, cost and carbon emissions analysis on 3D-printed molds for precast concrete and determined the method is economically beneficial compared to conventional wood molds.