
Filter News
Area of Research
- (-) Clean Energy (78)
- (-) Materials (37)
- (-) Supercomputing (2)
- Advanced Manufacturing (12)
- Biology and Environment (6)
- Building Technologies (1)
- Computer Science (2)
- Electricity and Smart Grid (1)
- Energy Sciences (1)
- Fusion and Fission (1)
- Fusion Energy (2)
- Isotopes (1)
- Materials for Computing (7)
- National Security (4)
- Neutron Science (28)
- Nuclear Science and Technology (2)
- Quantum information Science (1)
- Sensors and Controls (1)
- Transportation Systems (1)
News Type
News Topics
- (-) 3-D Printing/Advanced Manufacturing (36)
- (-) Composites (9)
- (-) Energy Storage (35)
- (-) Grid (21)
- (-) Materials Science (30)
- (-) Neutron Science (7)
- Advanced Reactors (2)
- Artificial Intelligence (2)
- Big Data (7)
- Bioenergy (5)
- Biology (4)
- Biomedical (7)
- Biotechnology (1)
- Buildings (19)
- Chemical Sciences (6)
- Clean Water (5)
- Climate Change (11)
- Computer Science (27)
- Coronavirus (9)
- Critical Materials (11)
- Cybersecurity (2)
- Decarbonization (12)
- Environment (27)
- Exascale Computing (2)
- Frontier (2)
- Fusion (4)
- High-Performance Computing (6)
- Hydropower (2)
- Isotopes (2)
- Machine Learning (3)
- Materials (28)
- Mathematics (2)
- Mercury (2)
- Microscopy (10)
- Molten Salt (1)
- Nanotechnology (12)
- National Security (1)
- Net Zero (2)
- Nuclear Energy (7)
- Physics (8)
- Polymers (10)
- Quantum Computing (5)
- Quantum Science (4)
- Security (2)
- Simulation (3)
- Space Exploration (4)
- Statistics (1)
- Summit (7)
- Sustainable Energy (34)
- Transportation (37)
Media Contacts
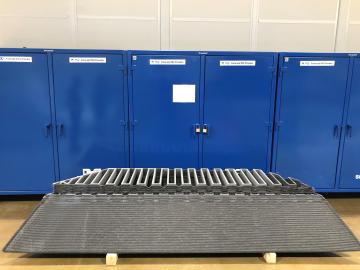
Oak Ridge National Laboratory researchers, in collaboration with Cincinnati Inc., demonstrated the potential for using multimaterials and recycled composites in large-scale applications by 3D printing a mold that replicated a single facet of a

In his career focused on energy storage science, Jianlin Li has learned that discovering new ways to process and assemble batteries is just as important as the development of new materials.
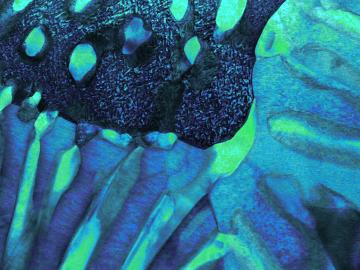
Oak Ridge National Laboratory scientists proved molybdenum titanium carbide, a refractory metal alloy that can withstand extreme temperature environments, can also be crack free and dense when produced with electron beam powder bed fusion.

Scientists at Oak Ridge National Laboratory have devised a method to identify the unique chemical makeup of every lithium-ion battery around the world, information that could accelerate recycling, recover critical materials and resolve a growing waste stream.
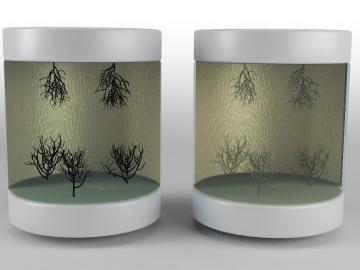
Scientists at Oak Ridge National Laboratory successfully demonstrated a technique to heal dendrites that formed in a solid electrolyte, resolving an issue that can hamper the performance of high energy-density, solid-state batteries.

Oak Ridge National Laboratory researchers combined additive manufacturing with conventional compression molding to produce high-performance thermoplastic composites reinforced with short carbon fibers.

A team of Oak Ridge National Laboratory researchers demonstrated that an additively manufactured hot stamping die – a tool used to create car body components – cooled faster than those produced by conventional manufacturing methods.

A method developed at Oak Ridge National Laboratory to print high-fidelity, passive sensors for energy applications can reduce the cost of monitoring critical power grid assets.
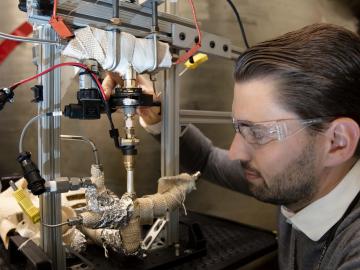
For a researcher who started out in mechanical engineering with a focus on engine combustion, Martin Wissink has learned a lot about neutrons on the job

Oak Ridge National Laboratory researchers have demonstrated that a new class of superalloys made of cobalt and nickel remains crack-free and defect-resistant in extreme heat, making them conducive for use in metal-based 3D printing applications.