Filter News
Area of Research
- (-) Advanced Manufacturing (15)
- (-) Isotopes (5)
- Biological Systems (2)
- Biology and Environment (32)
- Building Technologies (7)
- Chemical and Engineering Materials (1)
- Clean Energy (152)
- Climate and Environmental Systems (4)
- Computational Biology (1)
- Computational Engineering (2)
- Computer Science (10)
- Electricity and Smart Grid (1)
- Energy Sciences (2)
- Fossil Energy (1)
- Fusion and Fission (4)
- Fusion Energy (8)
- Isotope Development and Production (1)
- Materials (75)
- Materials for Computing (10)
- Mathematics (1)
- National Security (8)
- Neutron Data Analysis and Visualization (2)
- Neutron Science (35)
- Nuclear Science and Technology (18)
- Nuclear Systems Modeling, Simulation and Validation (2)
- Quantum information Science (3)
- Renewable Energy (2)
- Sensors and Controls (2)
- Supercomputing (41)
- Transportation Systems (2)
Media Contacts
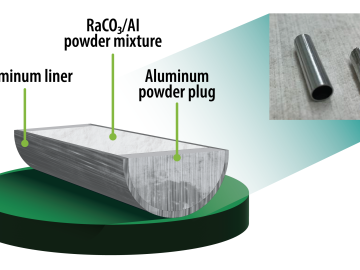
Oak Ridge National Laboratory researchers have developed a method to simplify one step of radioisotope production — and it’s faster and safer.

Oak Ridge National Laboratory scientists recently demonstrated a low-temperature, safe route to purifying molten chloride salts that minimizes their ability to corrode metals. This method could make the salts useful for storing energy generated from the sun’s heat.

Researchers at ORNL explored radium’s chemistry to advance cancer treatments using ionizing radiation.
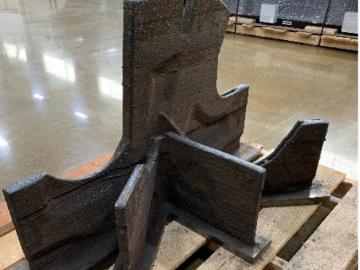
Oak Ridge National Laboratory researchers recently used large-scale additive manufacturing with metal to produce a full-strength steel component for a wind turbine, proving the technique as a viable alternative to

Oak Ridge National Laboratory researchers determined that designing polymers specifically with upcycling in mind could reduce future plastic waste considerably and facilitate a circular economy where the material is used repeatedly.

Oak Ridge National Laboratory researchers have developed a novel process to manufacture extreme heat resistant carbon-carbon composites. The performance of these materials will be tested in a U.S. Navy rocket that NASA will launch this fall.

A research team at Oak Ridge National Laboratory have 3D printed a thermal protection shield, or TPS, for a capsule that will launch with the Cygnus cargo spacecraft as part of the supply mission to the International Space Station.

An Oak Ridge National Laboratory researcher has invented a version of an isotope-separating device that can withstand extreme environments, including radiation and chemical solvents.

Oak Ridge National Laboratory researchers combined additive manufacturing with conventional compression molding to produce high-performance thermoplastic composites reinforced with short carbon fibers.

A team of Oak Ridge National Laboratory researchers demonstrated that an additively manufactured hot stamping die – a tool used to create car body components – cooled faster than those produced by conventional manufacturing methods.