Filter News
Area of Research
News Topics
- (-) Big Data (15)
- (-) Composites (9)
- (-) Statistics (1)
- 3-D Printing/Advanced Manufacturing (31)
- Advanced Reactors (13)
- Artificial Intelligence (13)
- Bioenergy (15)
- Biology (17)
- Biomedical (11)
- Biotechnology (3)
- Buildings (18)
- Chemical Sciences (8)
- Clean Water (13)
- Climate Change (21)
- Computer Science (39)
- Coronavirus (11)
- Critical Materials (12)
- Cybersecurity (3)
- Decarbonization (8)
- Energy Storage (31)
- Environment (43)
- Exascale Computing (1)
- Frontier (1)
- Fusion (9)
- Grid (20)
- High-Performance Computing (11)
- Hydropower (6)
- Irradiation (2)
- Isotopes (5)
- ITER (3)
- Machine Learning (10)
- Materials (35)
- Materials Science (33)
- Mathematics (1)
- Mercury (3)
- Microscopy (11)
- Molten Salt (5)
- Nanotechnology (12)
- National Security (3)
- Net Zero (1)
- Neutron Science (27)
- Nuclear Energy (18)
- Partnerships (1)
- Physics (4)
- Polymers (9)
- Quantum Computing (4)
- Quantum Science (10)
- Security (1)
- Simulation (6)
- Space Exploration (10)
- Summit (6)
- Sustainable Energy (44)
- Transportation (35)
Media Contacts

A research team at Oak Ridge National Laboratory have 3D printed a thermal protection shield, or TPS, for a capsule that will launch with the Cygnus cargo spacecraft as part of the supply mission to the International Space Station.

Researchers at Oak Ridge National Laboratory have developed a nationwide modeling tool to help infrastructure planners decide where and when to locate electric vehicle charging stations along interstate highways. The goal is to encourage the adoption of EVs for cross-country travel.
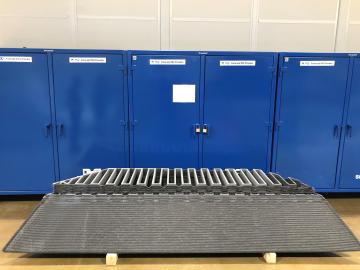
Oak Ridge National Laboratory researchers, in collaboration with Cincinnati Inc., demonstrated the potential for using multimaterials and recycled composites in large-scale applications by 3D printing a mold that replicated a single facet of a

Oak Ridge National Laboratory researchers combined additive manufacturing with conventional compression molding to produce high-performance thermoplastic composites reinforced with short carbon fibers.
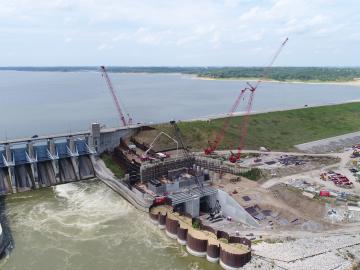
A new Department of Energy report produced by Oak Ridge National Laboratory details national and international trends in hydropower, including the role waterpower plays in enhancing the flexibility and resilience of the power grid.
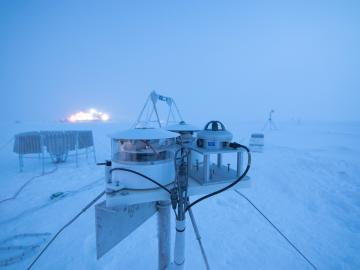
Researchers at Oak Ridge National Laboratory were part of an international team that collected a treasure trove of data measuring precipitation, air particles, cloud patterns and the exchange of energy between the atmosphere and the sea ice.
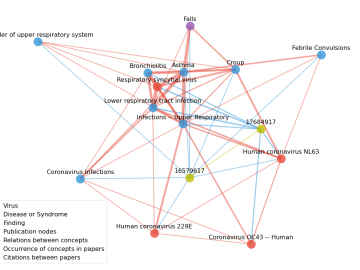
Scientists have tapped the immense power of the Summit supercomputer at Oak Ridge National Laboratory to comb through millions of medical journal articles to identify potential vaccines, drugs and effective measures that could suppress or stop the
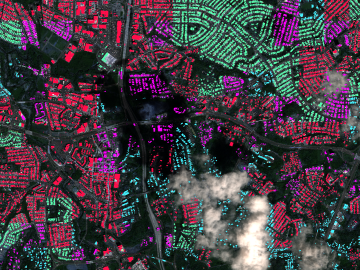
A novel approach developed by scientists at ORNL can scan massive datasets of large-scale satellite images to more accurately map infrastructure – such as buildings and roads – in hours versus days.

In collaboration with the Department of Veterans Affairs, a team at Oak Ridge National Laboratory has expanded a VA-developed predictive computing model to identify veterans at risk of suicide and sped it up to run 300 times faster, a gain that could profoundly affect the VA’s ability to reach susceptible veterans quickly.

A team including Oak Ridge National Laboratory and University of Tennessee researchers demonstrated a novel 3D printing approach called Z-pinning that can increase the material’s strength and toughness by more than three and a half times compared to conventional additive manufacturing processes.