Filter News
Area of Research
News Topics
- (-) Chemical Sciences (8)
- (-) Composites (9)
- (-) Molten Salt (5)
- 3-D Printing/Advanced Manufacturing (31)
- Advanced Reactors (13)
- Artificial Intelligence (13)
- Big Data (15)
- Bioenergy (15)
- Biology (17)
- Biomedical (11)
- Biotechnology (3)
- Buildings (18)
- Clean Water (13)
- Climate Change (21)
- Computer Science (39)
- Coronavirus (11)
- Critical Materials (12)
- Cybersecurity (3)
- Decarbonization (8)
- Energy Storage (31)
- Environment (43)
- Exascale Computing (1)
- Frontier (1)
- Fusion (9)
- Grid (20)
- High-Performance Computing (11)
- Hydropower (6)
- Irradiation (2)
- Isotopes (5)
- ITER (3)
- Machine Learning (10)
- Materials (35)
- Materials Science (33)
- Mathematics (1)
- Mercury (3)
- Microscopy (11)
- Nanotechnology (12)
- National Security (3)
- Net Zero (1)
- Neutron Science (27)
- Nuclear Energy (18)
- Partnerships (1)
- Physics (4)
- Polymers (9)
- Quantum Computing (4)
- Quantum Science (10)
- Security (1)
- Simulation (6)
- Space Exploration (10)
- Statistics (1)
- Summit (6)
- Sustainable Energy (44)
- Transportation (35)
Media Contacts

Several electrolyte and thin-film coating technologies, developed at Oak Ridge National Laboratory, have been licensed by BTRY, a battery technology company based in Virginia, to make batteries with increased energy density, at lower cost, and with an improved safety profile in crashes.

A research team at Oak Ridge National Laboratory have 3D printed a thermal protection shield, or TPS, for a capsule that will launch with the Cygnus cargo spacecraft as part of the supply mission to the International Space Station.

Oak Ridge National Laboratory researchers have developed a new catalyst for converting ethanol into C3+ olefins – the chemical
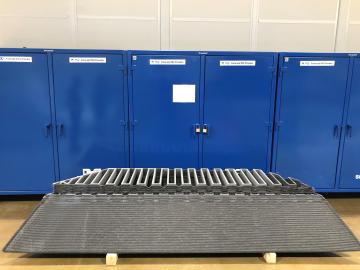
Oak Ridge National Laboratory researchers, in collaboration with Cincinnati Inc., demonstrated the potential for using multimaterials and recycled composites in large-scale applications by 3D printing a mold that replicated a single facet of a

Oak Ridge National Laboratory researchers combined additive manufacturing with conventional compression molding to produce high-performance thermoplastic composites reinforced with short carbon fibers.

In the 1960s, Oak Ridge National Laboratory's four-year Molten Salt Reactor Experiment tested the viability of liquid fuel reactors for commercial power generation. Results from that historic experiment recently became the basis for the first-ever molten salt reactor benchmark.

A team including Oak Ridge National Laboratory and University of Tennessee researchers demonstrated a novel 3D printing approach called Z-pinning that can increase the material’s strength and toughness by more than three and a half times compared to conventional additive manufacturing processes.
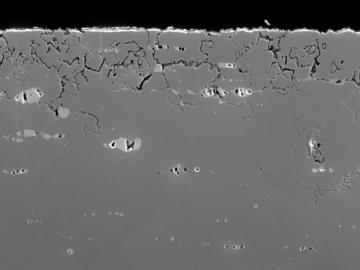
Oak Ridge National Laboratory scientists analyzed more than 50 years of data showing puzzlingly inconsistent trends about corrosion of structural alloys in molten salts and found one factor mattered most—salt purity.

Scientists from Oak Ridge National Laboratory performed a corrosion test in a neutron radiation field to support the continued development of molten salt reactors.

Experts focused on the future of nuclear technology will gather at Oak Ridge National Laboratory for the fourth annual Molten Salt Reactor Workshop on October 3–4.