Filter News
Area of Research
- (-) Advanced Manufacturing (5)
- (-) National Security (3)
- (-) Nuclear Science and Technology (3)
- Biology and Environment (6)
- Clean Energy (26)
- Computer Science (1)
- Electricity and Smart Grid (1)
- Functional Materials for Energy (1)
- Fusion and Fission (4)
- Fusion Energy (2)
- Isotope Development and Production (1)
- Isotopes (2)
- Materials (78)
- Materials Characterization (1)
- Materials for Computing (15)
- Materials Under Extremes (1)
- Neutron Science (23)
- Supercomputing (16)
- Transportation Systems (1)
News Topics
- (-) Materials Science (11)
- 3-D Printing/Advanced Manufacturing (27)
- Advanced Reactors (13)
- Artificial Intelligence (13)
- Big Data (6)
- Bioenergy (5)
- Biology (5)
- Biomedical (4)
- Biotechnology (1)
- Buildings (1)
- Chemical Sciences (2)
- Climate Change (5)
- Composites (3)
- Computer Science (22)
- Coronavirus (3)
- Cybersecurity (20)
- Decarbonization (3)
- Energy Storage (2)
- Environment (6)
- Exascale Computing (1)
- Frontier (1)
- Fusion (10)
- Grid (6)
- High-Performance Computing (4)
- Isotopes (5)
- Machine Learning (13)
- Materials (8)
- Molten Salt (4)
- Nanotechnology (1)
- National Security (34)
- Neutron Science (11)
- Nuclear Energy (41)
- Partnerships (4)
- Physics (3)
- Quantum Science (1)
- Security (11)
- Simulation (1)
- Space Exploration (6)
- Summit (2)
- Sustainable Energy (9)
- Transformational Challenge Reactor (4)
- Transportation (2)
Media Contacts

Scientists at ORNL have developed 3D-printed collimator techniques that can be used to custom design collimators that better filter out noise during different types of neutron scattering experiments

Oak Ridge National Laboratory researchers have demonstrated that a new class of superalloys made of cobalt and nickel remains crack-free and defect-resistant in extreme heat, making them conducive for use in metal-based 3D printing applications.

Six ORNL scientists have been elected as fellows to the American Association for the Advancement of Science, or AAAS.

From materials science and earth system modeling to quantum information science and cybersecurity, experts in many fields run simulations and conduct experiments to collect the abundance of data necessary for scientific progress.
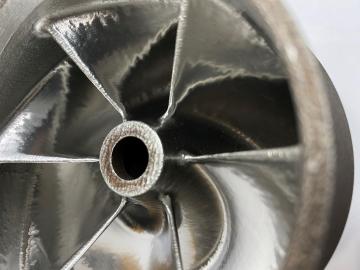
Scientists at the Department of Energy Manufacturing Demonstration Facility at ORNL have their eyes on the prize: the Transformational Challenge Reactor, or TCR, a microreactor built using 3D printing and other new approaches that will be up and running by 2023.

Research by an international team led by Duke University and the Department of Energy’s Oak Ridge National Laboratory scientists could speed the way to safer rechargeable batteries for consumer electronics such as laptops and cellphones.
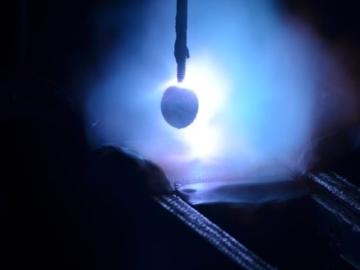
Researchers at Oak Ridge National Laboratory demonstrated that an additively manufactured polymer layer, when applied to carbon fiber reinforced plastic, or CFRP, can serve as an effective protector against aircraft lightning strikes.

A team including Oak Ridge National Laboratory and University of Tennessee researchers demonstrated a novel 3D printing approach called Z-pinning that can increase the material’s strength and toughness by more than three and a half times compared to conventional additive manufacturing processes.

Using additive manufacturing, scientists experimenting with tungsten at Oak Ridge National Laboratory hope to unlock new potential of the high-performance heat-transferring material used to protect components from the plasma inside a fusion reactor. Fusion requires hydrogen isotopes to reach millions of degrees.

A tiny vial of gray powder produced at the Department of Energy’s Oak Ridge National Laboratory is the backbone of a new experiment to study the intense magnetic fields created in nuclear collisions.