Filter News
Area of Research
- (-) Fusion and Fission (4)
- (-) Neutron Science (16)
- Advanced Manufacturing (22)
- Biology and Environment (16)
- Building Technologies (1)
- Clean Energy (84)
- Energy Frontier Research Centers (1)
- Fusion Energy (1)
- Materials (62)
- Materials for Computing (10)
- National Security (3)
- Nuclear Science and Technology (4)
- Quantum information Science (1)
- Supercomputing (33)
News Topics
- (-) 3-D Printing/Advanced Manufacturing (9)
- (-) Nanotechnology (11)
- (-) Quantum Computing (1)
- Advanced Reactors (7)
- Artificial Intelligence (7)
- Big Data (2)
- Bioenergy (7)
- Biology (5)
- Biomedical (12)
- Biotechnology (1)
- Buildings (1)
- Chemical Sciences (6)
- Clean Water (2)
- Climate Change (1)
- Composites (2)
- Computer Science (14)
- Coronavirus (8)
- Critical Materials (1)
- Cybersecurity (1)
- Decarbonization (4)
- Energy Storage (10)
- Environment (10)
- Exascale Computing (1)
- Fossil Energy (2)
- Frontier (2)
- Fusion (22)
- Grid (2)
- High-Performance Computing (4)
- Isotopes (1)
- ITER (6)
- Machine Learning (3)
- Materials (14)
- Materials Science (24)
- Mathematics (1)
- Microscopy (4)
- National Security (2)
- Net Zero (1)
- Neutron Science (99)
- Nuclear Energy (29)
- Partnerships (3)
- Physics (10)
- Polymers (1)
- Quantum Science (7)
- Security (3)
- Simulation (3)
- Space Exploration (3)
- Summit (6)
- Sustainable Energy (6)
- Transportation (7)
Media Contacts

Scientists at ORNL have developed 3D-printed collimator techniques that can be used to custom design collimators that better filter out noise during different types of neutron scattering experiments

ORNL’s Fulvia Pilat and Karren More recently participated in the inaugural 2023 Nanotechnology Infrastructure Leaders Summit and Workshop at the White House.
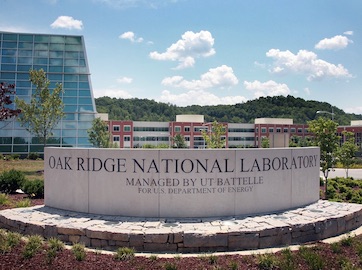
The Department of Energy’s Office of Science has selected three ORNL research teams to receive funding through DOE’s new Biopreparedness Research Virtual Environment initiative.

A team led by the U.S. Department of Energy’s Oak Ridge National Laboratory demonstrated the viability of a “quantum entanglement witness” capable of proving the presence of entanglement between magnetic particles, or spins, in a quantum material.

ORNL's Larry Baylor and Andrew Lupini have been elected fellows of the American Physical Society.
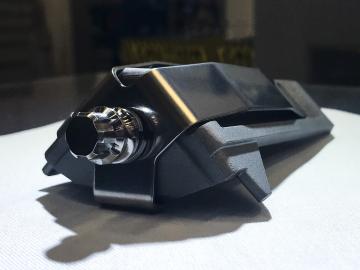
Four first-of-a-kind 3D-printed fuel assembly brackets, produced at the Department of Energy’s Manufacturing Demonstration Facility at Oak Ridge National Laboratory, have been installed and are now under routine operating

Scientists at ORNL and the University of Tennessee, Knoxville, have found a way to simultaneously increase the strength and ductility of an alloy by introducing tiny precipitates into its matrix and tuning their size and spacing.

At the Department of Energy’s Oak Ridge National Laboratory, scientists use artificial intelligence, or AI, to accelerate the discovery and development of materials for energy and information technologies.

Twenty-seven ORNL researchers Zoomed into 11 middle schools across Tennessee during the annual Engineers Week in February. East Tennessee schools throughout Oak Ridge and Roane, Sevier, Blount and Loudon counties participated, with three West Tennessee schools joining in.
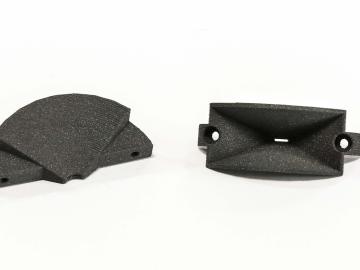
The ExOne Company, the global leader in industrial sand and metal 3D printers using binder jetting technology, announced it has reached a commercial license agreement with Oak Ridge National Laboratory to 3D print parts in aluminum-infiltrated boron carbide.