
Filter News
Area of Research
- (-) Clean Energy (88)
- (-) Materials (91)
- Advanced Manufacturing (6)
- Biological Systems (2)
- Biology and Environment (63)
- Biology and Soft Matter (1)
- Computational Biology (1)
- Electricity and Smart Grid (1)
- Functional Materials for Energy (1)
- Fusion and Fission (5)
- Materials for Computing (14)
- National Security (8)
- Neutron Science (102)
- Nuclear Science and Technology (9)
- Quantum information Science (2)
- Supercomputing (30)
- Transportation Systems (1)
News Topics
- (-) Bioenergy (30)
- (-) Composites (19)
- (-) Decarbonization (34)
- (-) Microscopy (29)
- (-) Molten Salt (3)
- (-) Neutron Science (42)
- (-) Polymers (21)
- 3-D Printing/Advanced Manufacturing (89)
- Advanced Reactors (9)
- Artificial Intelligence (13)
- Big Data (7)
- Biology (12)
- Biomedical (10)
- Biotechnology (4)
- Buildings (36)
- Chemical Sciences (33)
- Clean Water (10)
- Climate Change (23)
- Computer Science (36)
- Coronavirus (14)
- Critical Materials (19)
- Cybersecurity (10)
- Energy Storage (86)
- Environment (64)
- Exascale Computing (3)
- Fossil Energy (2)
- Frontier (3)
- Fusion (7)
- Grid (41)
- High-Performance Computing (9)
- Hydropower (2)
- Irradiation (1)
- Isotopes (13)
- ITER (1)
- Machine Learning (10)
- Materials (94)
- Materials Science (90)
- Mathematics (3)
- Mercury (3)
- Microelectronics (1)
- Nanotechnology (41)
- National Security (6)
- Net Zero (3)
- Nuclear Energy (22)
- Partnerships (16)
- Physics (29)
- Quantum Computing (3)
- Quantum Science (12)
- Renewable Energy (1)
- Security (7)
- Simulation (4)
- Space Exploration (5)
- Statistics (1)
- Summit (6)
- Sustainable Energy (71)
- Transformational Challenge Reactor (5)
- Transportation (69)
Media Contacts

A research team at Oak Ridge National Laboratory have 3D printed a thermal protection shield, or TPS, for a capsule that will launch with the Cygnus cargo spacecraft as part of the supply mission to the International Space Station.

David Sholl has come to the U.S. Department of Energy’s Oak Ridge National Laboratory with a wealth of scientific expertise and a personal mission: hasten the development and deployment of decarbonization solutions for the nation’s energy system.

Scientists at ORNL and the University of Tennessee, Knoxville, have found a way to simultaneously increase the strength and ductility of an alloy by introducing tiny precipitates into its matrix and tuning their size and spacing.
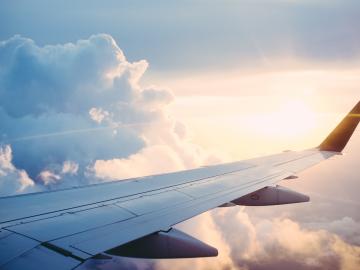
ORNL’s Zhenglong Li led a team tasked with improving the current technique for converting ethanol to C3+ olefins and demonstrated a unique composite catalyst that upends current practice and drives down costs. The research was published in ACS Catalysis.
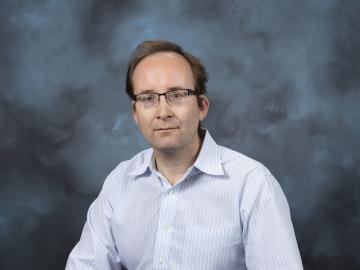
Sergei Kalinin, a scientist and inventor at the Department of Energy’s Oak Ridge National Laboratory, has been elected a fellow of the Microscopy Society of America professional society.
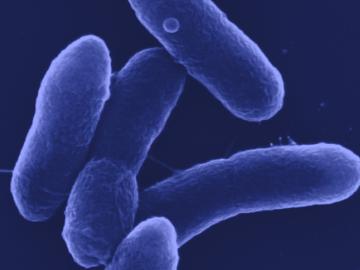
A research team led by Oak Ridge National Laboratory bioengineered a microbe to efficiently turn waste into itaconic acid, an industrial chemical used in plastics and paints.
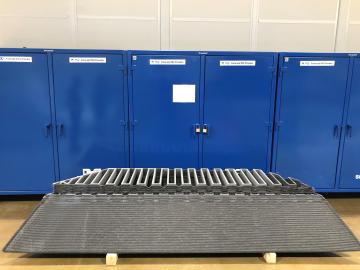
Oak Ridge National Laboratory researchers, in collaboration with Cincinnati Inc., demonstrated the potential for using multimaterials and recycled composites in large-scale applications by 3D printing a mold that replicated a single facet of a

At the Department of Energy’s Oak Ridge National Laboratory, scientists use artificial intelligence, or AI, to accelerate the discovery and development of materials for energy and information technologies.
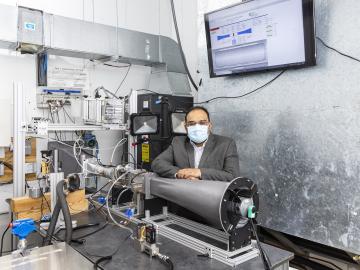
When Kashif Nawaz looks at a satellite map of the U.S., he sees millions of buildings that could hold a potential solution for the capture of carbon dioxide, a plentiful gas that can be harmful when excessive amounts are released into the atmosphere, raising the Earth’s temperature.

Oak Ridge National Laboratory researchers combined additive manufacturing with conventional compression molding to produce high-performance thermoplastic composites reinforced with short carbon fibers.