
Filter News
Area of Research
- (-) Clean Energy (81)
- Advanced Manufacturing (8)
- Biological Systems (2)
- Biology and Environment (71)
- Building Technologies (1)
- Climate and Environmental Systems (1)
- Computational Biology (2)
- Computational Engineering (3)
- Computer Science (16)
- Electricity and Smart Grid (1)
- Functional Materials for Energy (1)
- Fusion and Fission (8)
- Fusion Energy (4)
- Isotope Development and Production (1)
- Isotopes (2)
- Materials (123)
- Materials Characterization (1)
- Materials for Computing (20)
- Materials Under Extremes (1)
- Mathematics (1)
- National Security (24)
- Neutron Science (45)
- Nuclear Science and Technology (8)
- Quantum information Science (7)
- Supercomputing (139)
- Transportation Systems (1)
News Topics
- (-) Bioenergy (26)
- (-) Composites (17)
- (-) Computer Science (25)
- (-) Frontier (2)
- (-) Materials Science (26)
- (-) Physics (1)
- (-) Summit (4)
- 3-D Printing/Advanced Manufacturing (78)
- Advanced Reactors (6)
- Artificial Intelligence (8)
- Big Data (5)
- Biology (11)
- Biomedical (6)
- Biotechnology (4)
- Buildings (36)
- Chemical Sciences (14)
- Clean Water (8)
- Climate Change (21)
- Coronavirus (12)
- Critical Materials (9)
- Cybersecurity (8)
- Decarbonization (33)
- Energy Storage (72)
- Environment (54)
- Exascale Computing (2)
- Fossil Energy (2)
- Fusion (1)
- Grid (40)
- High-Performance Computing (6)
- Hydropower (2)
- Isotopes (1)
- Machine Learning (7)
- Materials (35)
- Mathematics (2)
- Mercury (3)
- Microelectronics (1)
- Microscopy (8)
- Molten Salt (1)
- Nanotechnology (8)
- National Security (5)
- Net Zero (3)
- Neutron Science (11)
- Nuclear Energy (7)
- Partnerships (12)
- Polymers (11)
- Quantum Science (2)
- Renewable Energy (1)
- Security (6)
- Simulation (4)
- Space Exploration (3)
- Statistics (1)
- Sustainable Energy (69)
- Transformational Challenge Reactor (3)
- Transportation (65)
Media Contacts

Oak Ridge National Laboratory researchers combined additive manufacturing with conventional compression molding to produce high-performance thermoplastic composites reinforced with short carbon fibers.

Twenty-seven ORNL researchers Zoomed into 11 middle schools across Tennessee during the annual Engineers Week in February. East Tennessee schools throughout Oak Ridge and Roane, Sevier, Blount and Loudon counties participated, with three West Tennessee schools joining in.

Oak Ridge National Laboratory researchers have demonstrated that a new class of superalloys made of cobalt and nickel remains crack-free and defect-resistant in extreme heat, making them conducive for use in metal-based 3D printing applications.

Three technologies developed by ORNL researchers have won National Technology Transfer Awards from the Federal Laboratory Consortium. One of the awards went to a team that adapted melt-blowing capabilities at DOE’s Carbon Fiber Technology Facility to enable the production of filter material for N95 masks in the fight against COVID-19.
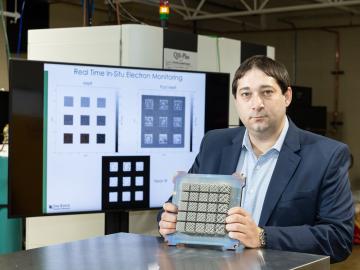
Growing up in the heart of the American automobile industry near Detroit, Oak Ridge National Laboratory materials scientist Mike Kirka was no stranger to manufacturing.


Six scientists at the Department of Energy’s Oak Ridge National Laboratory were named Battelle Distinguished Inventors, in recognition of obtaining 14 or more patents during their careers at the lab.

As ORNL’s fuel properties technical lead for the U.S. Department of Energy’s Co-Optimization of Fuel and Engines, or Co-Optima, initiative, Jim Szybist has been on a quest for the past few years to identify the most significant indicators for predicting how a fuel will perform in engines designed for light-duty vehicles such as passenger cars and pickup trucks.

Seven ORNL scientists have been named among the 2020 Highly Cited Researchers list, according to Clarivate, a data analytics firm that specializes in scientific and academic research.
A collaboration between the ORNL and a Florida-based medical device manufacturer has led to the addition of 500 jobs in the Miami area to support the mass production of N95 respirator masks.