Filter News
Area of Research
- (-) Advanced Manufacturing (5)
- (-) Fusion and Fission (4)
- Biology and Environment (6)
- Clean Energy (26)
- Computer Science (1)
- Electricity and Smart Grid (1)
- Functional Materials for Energy (1)
- Fusion Energy (2)
- Isotope Development and Production (1)
- Isotopes (2)
- Materials (78)
- Materials Characterization (1)
- Materials for Computing (15)
- Materials Under Extremes (1)
- National Security (3)
- Neutron Science (23)
- Nuclear Science and Technology (3)
- Supercomputing (16)
- Transportation Systems (1)
News Topics
- (-) Materials Science (9)
- 3-D Printing/Advanced Manufacturing (25)
- Advanced Reactors (7)
- Artificial Intelligence (2)
- Bioenergy (2)
- Biology (1)
- Biomedical (1)
- Buildings (1)
- Chemical Sciences (4)
- Composites (4)
- Computer Science (3)
- Critical Materials (1)
- Cybersecurity (1)
- Decarbonization (2)
- Energy Storage (4)
- Environment (2)
- Exascale Computing (1)
- Fossil Energy (1)
- Frontier (1)
- Fusion (23)
- Grid (2)
- High-Performance Computing (2)
- Isotopes (1)
- ITER (6)
- Machine Learning (1)
- Materials (7)
- Microscopy (1)
- Nanotechnology (1)
- Net Zero (1)
- Neutron Science (3)
- Nuclear Energy (28)
- Partnerships (3)
- Physics (1)
- Security (2)
- Simulation (3)
- Space Exploration (2)
- Sustainable Energy (9)
- Transformational Challenge Reactor (1)
- Transportation (2)
Media Contacts

Scientists at ORNL have developed 3D-printed collimator techniques that can be used to custom design collimators that better filter out noise during different types of neutron scattering experiments

ORNL has entered a strategic research partnership with the United Kingdom Atomic Energy Authority, or UKAEA, to investigate how different types of materials behave under the influence of high-energy neutron sources. The $4 million project is part of UKAEA's roadmap program, which aims to produce electricity from fusion.

Three researchers at ORNL have been named ORNL Corporate Fellows in recognition of significant career accomplishments and continued leadership in their scientific fields.

More than 50 current employees and recent retirees from ORNL received Department of Energy Secretary’s Honor Awards from Secretary Jennifer Granholm in January as part of project teams spanning the national laboratory system. The annual awards recognized 21 teams and three individuals for service and contributions to DOE’s mission and to the benefit of the nation.

The Department of Energy’s Office of Science has selected five Oak Ridge National Laboratory scientists for Early Career Research Program awards.

Oak Ridge National Laboratory researchers have demonstrated that a new class of superalloys made of cobalt and nickel remains crack-free and defect-resistant in extreme heat, making them conducive for use in metal-based 3D printing applications.
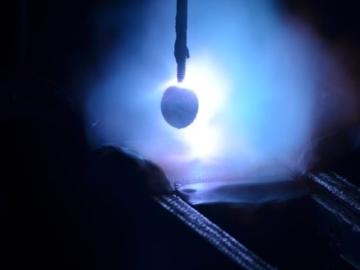
Researchers at Oak Ridge National Laboratory demonstrated that an additively manufactured polymer layer, when applied to carbon fiber reinforced plastic, or CFRP, can serve as an effective protector against aircraft lightning strikes.

A team including Oak Ridge National Laboratory and University of Tennessee researchers demonstrated a novel 3D printing approach called Z-pinning that can increase the material’s strength and toughness by more than three and a half times compared to conventional additive manufacturing processes.

Using additive manufacturing, scientists experimenting with tungsten at Oak Ridge National Laboratory hope to unlock new potential of the high-performance heat-transferring material used to protect components from the plasma inside a fusion reactor. Fusion requires hydrogen isotopes to reach millions of degrees.