
Filter News
Area of Research
- (-) Advanced Manufacturing (22)
- (-) Materials (73)
- Biological Systems (1)
- Biology and Environment (43)
- Building Technologies (1)
- Clean Energy (173)
- Computational Biology (2)
- Computational Engineering (2)
- Computer Science (8)
- Electricity and Smart Grid (3)
- Energy Sciences (1)
- Functional Materials for Energy (2)
- Fusion and Fission (10)
- Fusion Energy (1)
- Isotope Development and Production (1)
- Isotopes (28)
- Materials for Computing (9)
- National Security (29)
- Neutron Science (26)
- Nuclear Science and Technology (13)
- Quantum information Science (2)
- Sensors and Controls (1)
- Supercomputing (67)
News Topics
- (-) 3-D Printing/Advanced Manufacturing (42)
- (-) Big Data (2)
- (-) Biomedical (7)
- (-) Cybersecurity (4)
- (-) Energy Storage (34)
- (-) Exascale Computing (2)
- (-) Grid (5)
- (-) Isotopes (13)
- (-) Space Exploration (3)
- Advanced Reactors (4)
- Artificial Intelligence (10)
- Bioenergy (11)
- Biology (4)
- Buildings (5)
- Chemical Sciences (32)
- Clean Water (3)
- Climate Change (5)
- Composites (12)
- Computer Science (17)
- Coronavirus (4)
- Critical Materials (13)
- Decarbonization (7)
- Environment (15)
- Frontier (3)
- Fusion (7)
- High-Performance Computing (4)
- Irradiation (1)
- ITER (1)
- Machine Learning (6)
- Materials (79)
- Materials Science (81)
- Mathematics (1)
- Microscopy (27)
- Molten Salt (3)
- Nanotechnology (39)
- National Security (3)
- Net Zero (1)
- Neutron Science (35)
- Nuclear Energy (17)
- Partnerships (11)
- Physics (29)
- Polymers (17)
- Quantum Computing (3)
- Quantum Science (11)
- Renewable Energy (1)
- Security (2)
- Simulation (1)
- Summit (2)
- Sustainable Energy (16)
- Transformational Challenge Reactor (4)
- Transportation (14)
Media Contacts

Oak Ridge National Laboratory researchers combined additive manufacturing with conventional compression molding to produce high-performance thermoplastic composites reinforced with short carbon fibers.

A team of Oak Ridge National Laboratory researchers demonstrated that an additively manufactured hot stamping die – a tool used to create car body components – cooled faster than those produced by conventional manufacturing methods.

Oak Ridge National Laboratory researchers have demonstrated that a new class of superalloys made of cobalt and nickel remains crack-free and defect-resistant in extreme heat, making them conducive for use in metal-based 3D printing applications.

On Feb. 18, the world will be watching as NASA’s Perseverance rover makes its final descent into Jezero Crater on the surface of Mars. Mars 2020 is the first NASA mission that uses plutonium-238 produced at the Department of Energy’s Oak Ridge National Laboratory.
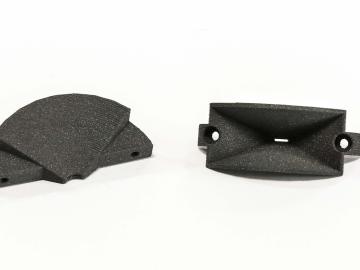
The ExOne Company, the global leader in industrial sand and metal 3D printers using binder jetting technology, announced it has reached a commercial license agreement with Oak Ridge National Laboratory to 3D print parts in aluminum-infiltrated boron carbide.

Six scientists at the Department of Energy’s Oak Ridge National Laboratory were named Battelle Distinguished Inventors, in recognition of obtaining 14 or more patents during their careers at the lab.

Momentum Technologies Inc., a Dallas, Texas-based materials science company that is focused on extracting critical metals from electronic waste, has licensed an Oak Ridge National Laboratory process for recovering cobalt and other metals from spent
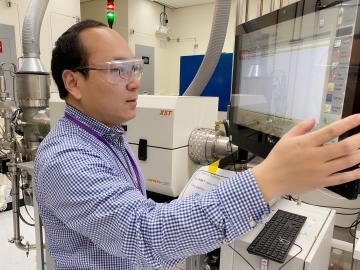
About 60 years ago, scientists discovered that a certain rare earth metal-hydrogen mixture, yttrium, could be the ideal moderator to go inside small, gas-cooled nuclear reactors.

A team led by Oak Ridge National Laboratory developed a novel, integrated approach to track energy-transporting ions within an ultra-thin material, which could unlock its energy storage potential leading toward faster charging, longer-lasting devices.
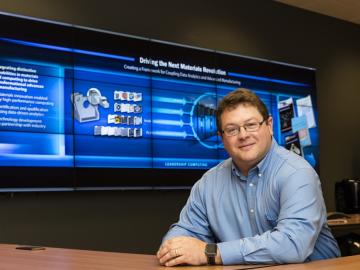
The Society of Manufacturing Engineers, known as SME, has named William Peter, director of Oak Ridge National Laboratory’s Manufacturing Demonstration Facility in the Energy and Environmental Sciences Directorate, among its 2020 College of SME Fellows.