Filter News
Area of Research
- (-) Materials (20)
- Biology and Environment (20)
- Biology and Soft Matter (1)
- Clean Energy (42)
- Electricity and Smart Grid (1)
- Functional Materials for Energy (1)
- Fusion and Fission (3)
- Materials for Computing (1)
- National Security (2)
- Neutron Science (2)
- Nuclear Science and Technology (1)
- Supercomputing (8)
- Transportation Systems (1)
News Topics
- (-) Critical Materials (13)
- (-) Decarbonization (7)
- 3-D Printing/Advanced Manufacturing (23)
- Advanced Reactors (4)
- Artificial Intelligence (9)
- Big Data (2)
- Bioenergy (11)
- Biology (4)
- Biomedical (7)
- Buildings (5)
- Chemical Sciences (32)
- Clean Water (3)
- Climate Change (5)
- Composites (9)
- Computer Science (17)
- Coronavirus (4)
- Cybersecurity (4)
- Energy Storage (34)
- Environment (15)
- Exascale Computing (2)
- Frontier (3)
- Fusion (7)
- Grid (5)
- High-Performance Computing (4)
- Irradiation (1)
- Isotopes (13)
- ITER (1)
- Machine Learning (5)
- Materials (73)
- Materials Science (78)
- Mathematics (1)
- Microscopy (27)
- Molten Salt (3)
- Nanotechnology (39)
- National Security (3)
- Net Zero (1)
- Neutron Science (33)
- Nuclear Energy (16)
- Partnerships (11)
- Physics (29)
- Polymers (17)
- Quantum Computing (3)
- Quantum Science (11)
- Renewable Energy (1)
- Security (2)
- Simulation (1)
- Space Exploration (2)
- Summit (2)
- Sustainable Energy (13)
- Transformational Challenge Reactor (3)
- Transportation (14)
Media Contacts

Oak Ridge National Laboratory scientists designed a recyclable polymer for carbon-fiber composites to enable circular manufacturing of parts that boost energy efficiency in automotive, wind power and aerospace applications.

Researchers at the Department of Energy’s Oak Ridge National Laboratory and their technologies have received seven 2022 R&D 100 Awards, plus special recognition for a battery-related green technology product.

Researchers at Oak Ridge National Laboratory and Momentum Technologies have piloted an industrial-scale process for recycling valuable materials in the millions of tons of e-waste generated annually in the United States.
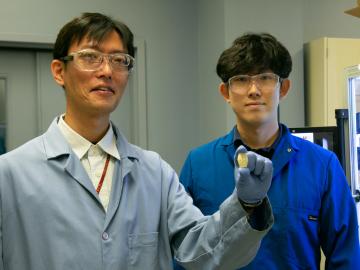
ORNL researchers have developed an upcycling approach that adds value to discarded plastics for reuse in additive manufacturing, or 3D printing.

Researchers at Oak Ridge National Laboratory are using state-of-the-art methods to shed light on chemical separations needed to recover rare-earth elements and secure critical materials for clean energy technologies.

A new technology for rare-earth elements chemical separation has been licensed to Marshallton Research Laboratories, a North Carolina-based manufacturer of organic chemicals for a range of industries.

Momentum Technologies Inc., a Dallas, Texas-based materials science company that is focused on extracting critical metals from electronic waste, has licensed an Oak Ridge National Laboratory process for recovering cobalt and other metals from spent

Real-time measurements captured by researchers at ORNL provide missing insight into chemical separations to recover cobalt, a critical raw material used to make batteries and magnets for modern technologies.
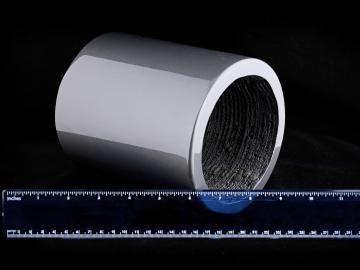
Researchers at the Department of Energy’s Oak Ridge National Laboratory have demonstrated that permanent magnets produced by additive manufacturing can outperform bonded magnets made using traditional techniques while conserving critical materials. Scientists fabric...
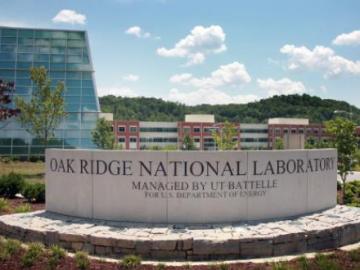
A new technology developed by the U.S. Department of Energy’s Critical Materials Institute that aids in the recycling, recovery and extraction of rare earth minerals has been licensed to U.S. Rare Earths, Inc.