
Filter News
Area of Research
- Advanced Manufacturing (22)
- Biological Systems (1)
- Biology and Environment (44)
- Biology and Soft Matter (1)
- Building Technologies (1)
- Clean Energy (95)
- Computational Biology (2)
- Computational Engineering (1)
- Fusion and Fission (8)
- Fusion Energy (1)
- Isotopes (5)
- Materials (55)
- Materials for Computing (8)
- National Security (6)
- Neutron Science (19)
- Nuclear Science and Technology (6)
- Supercomputing (27)
News Topics
- (-) 3-D Printing/Advanced Manufacturing (125)
- (-) Biomedical (60)
- (-) Biotechnology (23)
- (-) Chemical Sciences (70)
- Advanced Reactors (34)
- Artificial Intelligence (97)
- Big Data (60)
- Bioenergy (92)
- Biology (100)
- Buildings (61)
- Clean Water (31)
- Climate Change (104)
- Composites (29)
- Computer Science (195)
- Coronavirus (46)
- Critical Materials (29)
- Cybersecurity (35)
- Decarbonization (82)
- Education (4)
- Element Discovery (1)
- Emergency (2)
- Energy Storage (112)
- Environment (198)
- Exascale Computing (40)
- Fossil Energy (6)
- Frontier (44)
- Fusion (57)
- Grid (66)
- High-Performance Computing (90)
- Hydropower (11)
- Irradiation (3)
- Isotopes (55)
- ITER (7)
- Machine Learning (49)
- Materials (145)
- Materials Science (145)
- Mathematics (9)
- Mercury (12)
- Microelectronics (4)
- Microscopy (51)
- Molten Salt (8)
- Nanotechnology (60)
- National Security (71)
- Net Zero (14)
- Neutron Science (134)
- Nuclear Energy (110)
- Partnerships (49)
- Physics (63)
- Polymers (33)
- Quantum Computing (37)
- Quantum Science (71)
- Renewable Energy (2)
- Security (25)
- Simulation (49)
- Software (1)
- Space Exploration (25)
- Statistics (3)
- Summit (59)
- Sustainable Energy (130)
- Transformational Challenge Reactor (7)
- Transportation (97)
Media Contacts

To speed the arrival of the next-generation solid-state batteries that will power electric vehicles and other technologies, scientists led by ORNL advanced the development of flexible, durable sheets of electrolytes. They used a polymer to create a strong yet springy thin film that binds electrolytic particles and at least doubles energy storage.

Jeremiah Sewell leads a team at ORNL, working on xenon-129 production for lung imaging. Reflecting on his career, Sewell views each opportunity as a "door" he steps through, leveraging over 25 years of experience in nuclear power and centrifuge operations to advance the facility’s mission.
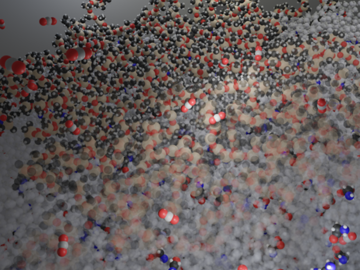
Researchers at ORNL have demonstrated that small molecular tweaks to surfaces can improve absorption technology for direct air capture of carbon dioxide. The team added a charged polymer layer to an amino acid solution, and then, through spectroscopy and simulation, found that the charged layer can hold amino acids at its surface.

Benjamin Manard, an analytical chemist in the Chemical Sciences Division of the Department of Energy’s Oak Ridge National Laboratory, will receive the 2024 Lester W. Strock Award from the Society of Applied Spectroscopy.
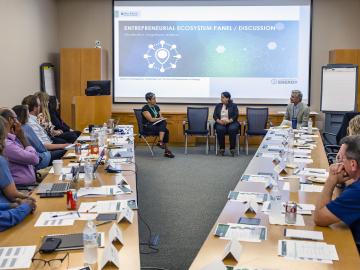
Five researchers at the Department of Energy’s Oak Ridge National Laboratory recently completed an eight-week pilot commercialization coaching program as part of Safari, a program funded by DOE’s Office of Technology Transitions, or OTT, Practices to Accelerate the Commercialization of Technologies, or PACT.
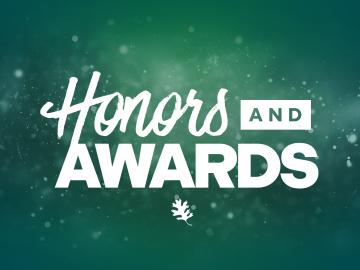
Two additive manufacturing researchers from ORNL received prestigious awards from national organizations. Amy Elliott and Nadim Hmeidat, who both work in the Manufacturing Science Division, were recognized recently for their early career accomplishments.
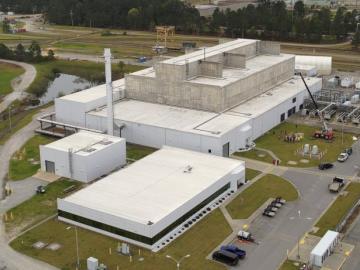
A team of federal contractor and national laboratory engineers and scientists from the U.S. Department of Energy Office of Environmental Management has been nationally distinguished as “Heroes of Chemistry” for making the world better through their effort, ingenuity, creativity and perseverance.

Brian Sanders is focused on impactful, multidisciplinary science at Oak Ridge National Laboratory, developing solutions for everything from improved imaging of plant-microbe interactions that influence ecosystem health to advancing new treatments for cancer and viral infections.

Brittany Rodriguez never imagined she would pursue a science career at a Department of Energy national laboratory. However, after some encouraging words from her mother, input from key mentors at the University of Texas Rio Grande Valley, or UTRGV, and a lot of hard work, Rodriguez landed at DOE’s Manufacturing Demonstration Facility, or MDF, at Oak Ridge National Laboratory.
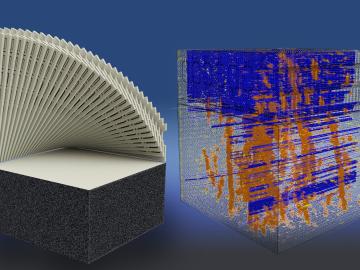
The Department of Energy’s Oak Ridge National Laboratory has publicly released a new set of additive manufacturing data that industry and researchers can use to evaluate and improve the quality of 3D-printed components. The breadth of the datasets can significantly boost efforts to verify the quality of additively manufactured parts using only information gathered during printing, without requiring expensive and time-consuming post-production analysis.