Filter News
Area of Research
- Advanced Manufacturing (22)
- Biology and Environment (83)
- Building Technologies (1)
- Clean Energy (86)
- Climate and Environmental Systems (1)
- Computational Biology (2)
- Fusion and Fission (5)
- Fusion Energy (1)
- Isotopes (24)
- Materials (38)
- Materials for Computing (6)
- National Security (7)
- Neutron Science (11)
- Nuclear Science and Technology (9)
- Supercomputing (16)
News Topics
- (-) 3-D Printing/Advanced Manufacturing (116)
- (-) Biology (96)
- (-) Isotopes (46)
- Advanced Reactors (33)
- Artificial Intelligence (84)
- Big Data (50)
- Bioenergy (88)
- Biomedical (58)
- Biotechnology (21)
- Buildings (54)
- Chemical Sciences (59)
- Clean Water (29)
- Climate Change (94)
- Composites (25)
- Computer Science (182)
- Coronavirus (46)
- Critical Materials (24)
- Cybersecurity (35)
- Decarbonization (73)
- Education (3)
- Element Discovery (1)
- Emergency (2)
- Energy Storage (106)
- Environment (192)
- Exascale Computing (34)
- Fossil Energy (5)
- Frontier (39)
- Fusion (53)
- Grid (59)
- High-Performance Computing (82)
- Hydropower (11)
- Irradiation (3)
- ITER (7)
- Machine Learning (44)
- Materials (140)
- Materials Science (134)
- Mathematics (6)
- Mercury (12)
- Microelectronics (2)
- Microscopy (50)
- Molten Salt (8)
- Nanotechnology (60)
- National Security (56)
- Net Zero (11)
- Neutron Science (129)
- Nuclear Energy (103)
- Partnerships (40)
- Physics (58)
- Polymers (31)
- Quantum Computing (28)
- Quantum Science (65)
- Renewable Energy (2)
- Security (23)
- Simulation (43)
- Software (1)
- Space Exploration (24)
- Statistics (3)
- Summit (57)
- Sustainable Energy (119)
- Transformational Challenge Reactor (7)
- Transportation (93)
Media Contacts
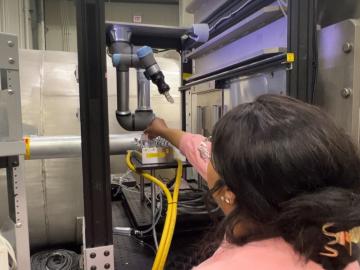
The BIO-SANS instrument, located at Oak Ridge National Laboratory’s High Flux Isotope Reactor, is the latest neutron scattering instrument to be retrofitted with state-of-the-art robotics and custom software. The sophisticated upgrade quadruples the number of samples the instrument can measure automatically and significantly reduces the need for human assistance.
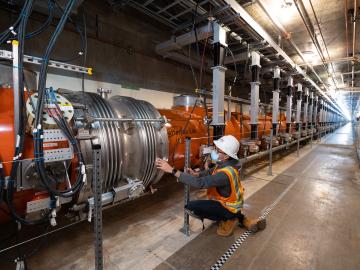
Plans to unite the capabilities of two cutting-edge technological facilities funded by the Department of Energy’s Office of Science promise to usher in a new era of dynamic structural biology. Through DOE’s Integrated Research Infrastructure, or IRI, initiative, the facilities will complement each other’s technologies in the pursuit of science despite being nearly 2,500 miles apart.

Computational scientists at ORNL have published a study that questions a long-accepted factor in simulating the molecular dynamics of water: the 2 femtosecond time step. According to the team’s findings, using anything greater than a 0.5 femtosecond time step can introduce errors in both the dynamics and thermodynamics when simulating water using a rigid-body description.
Simulations performed on the Summit supercomputer at ORNL are cutting through that time and expense by helping researchers digitally customize the ideal alloy.
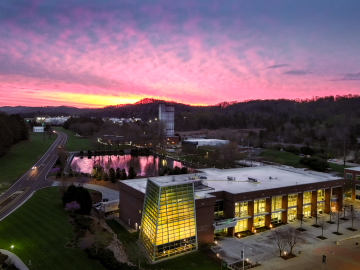
Rishi Pillai and his research team from ORNL will receive a Best Paper award from the American Society of Mechanical Engineers International Gas Turbine Institute in June at the Turbo Expo 2024 in London.
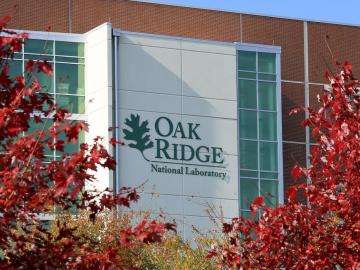
The Society of Manufacturing Engineers has honored three Oak Ridge National Laboratory researchers with the 2024 SME Susan Smyth Outstanding Young Manufacturing Engineer Award.
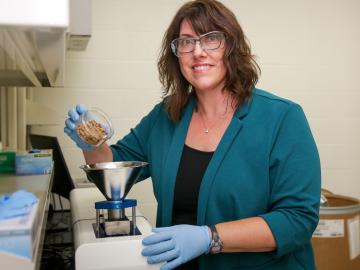
ORNL’s Erin Webb is co-leading a new Circular Bioeconomy Systems Convergent Research Initiative focused on advancing production and use of renewable carbon from Tennessee to meet societal needs.

A first-ever dataset bridging molecular information about the poplar tree microbiome to ecosystem-level processes has been released by a team of DOE scientists led by ORNL. The project aims to inform research regarding how natural systems function, their vulnerability to a changing climate and ultimately how plants might be engineered for better performance as sources of bioenergy and natural carbon storage.

Scientists at ORNL have developed 3D-printed collimator techniques that can be used to custom design collimators that better filter out noise during different types of neutron scattering experiments
ORNL scientists have determined how to avoid costly and potentially irreparable damage to large metallic parts fabricated through additive manufacturing, also known as 3D printing, that is caused by residual stress in the material.