
Filter News
Area of Research
- Advanced Manufacturing (22)
- Biology and Environment (12)
- Building Technologies (1)
- Clean Energy (86)
- Fusion and Fission (7)
- Fusion Energy (1)
- Isotope Development and Production (1)
- Isotopes (4)
- Materials (33)
- Materials for Computing (5)
- National Security (6)
- Neutron Science (9)
- Nuclear Science and Technology (9)
- Supercomputing (9)
News Topics
- (-) 3-D Printing/Advanced Manufacturing (122)
- (-) Partnerships (44)
- (-) Space Exploration (25)
- Advanced Reactors (34)
- Artificial Intelligence (91)
- Big Data (55)
- Bioenergy (92)
- Biology (99)
- Biomedical (58)
- Biotechnology (22)
- Buildings (57)
- Chemical Sciences (65)
- Clean Water (29)
- Climate Change (100)
- Composites (26)
- Computer Science (189)
- Coronavirus (46)
- Critical Materials (26)
- Cybersecurity (35)
- Decarbonization (80)
- Education (4)
- Element Discovery (1)
- Emergency (2)
- Energy Storage (109)
- Environment (195)
- Exascale Computing (37)
- Fossil Energy (6)
- Frontier (42)
- Fusion (55)
- Grid (63)
- High-Performance Computing (85)
- Hydropower (11)
- Irradiation (3)
- Isotopes (53)
- ITER (7)
- Machine Learning (48)
- Materials (144)
- Materials Science (141)
- Mathematics (8)
- Mercury (12)
- Microelectronics (3)
- Microscopy (51)
- Molten Salt (8)
- Nanotechnology (60)
- National Security (62)
- Net Zero (14)
- Neutron Science (131)
- Nuclear Energy (109)
- Physics (61)
- Polymers (33)
- Quantum Computing (34)
- Quantum Science (69)
- Renewable Energy (2)
- Security (24)
- Simulation (48)
- Software (1)
- Statistics (3)
- Summit (57)
- Sustainable Energy (126)
- Transformational Challenge Reactor (7)
- Transportation (97)
Media Contacts

The U.S. Environmental Protection Agency has approved the registration and use of a renewable gasoline blendstock developed by Vertimass LLC and ORNL that can significantly reduce the emissions profile of vehicles when added to conventional fuels.
Simulations performed on the Summit supercomputer at ORNL are cutting through that time and expense by helping researchers digitally customize the ideal alloy.
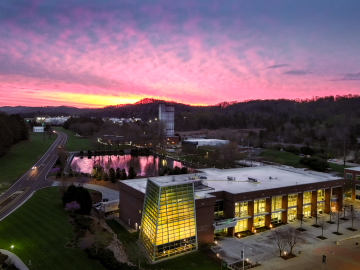
Rishi Pillai and his research team from ORNL will receive a Best Paper award from the American Society of Mechanical Engineers International Gas Turbine Institute in June at the Turbo Expo 2024 in London.
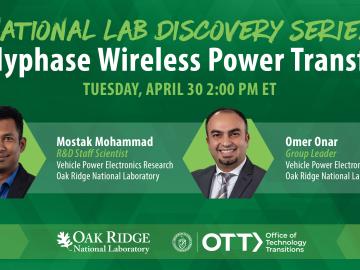
ORNL’s Omer Onar and Mostak Mohammad will present on ORNL's wireless charging technology in DOE’s Office of Technology Transitions National Lab Discovery Series Tuesday, April 30.
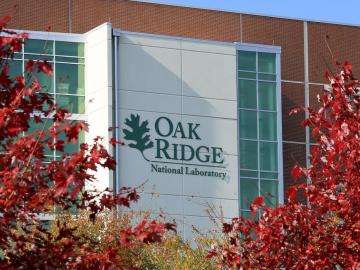
The Society of Manufacturing Engineers has honored three Oak Ridge National Laboratory researchers with the 2024 SME Susan Smyth Outstanding Young Manufacturing Engineer Award.
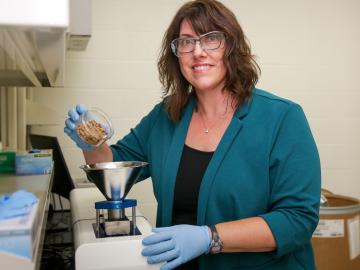
ORNL’s Erin Webb is co-leading a new Circular Bioeconomy Systems Convergent Research Initiative focused on advancing production and use of renewable carbon from Tennessee to meet societal needs.
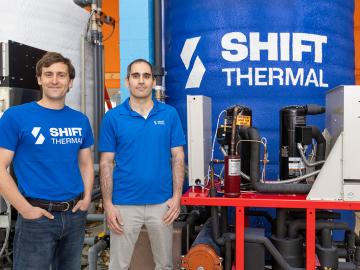
Shift Thermal, a member of Innovation Crossroads’ first cohort of fellows, is commercializing advanced ice thermal energy storage for HVAC, shifting the cooling process to be more sustainable, cost-effective and resilient. Shift Thermal wants to enable a lower-cost, more-efficient thermal energy storage method to provide long-duration resilient cooling when the electric grid is down.
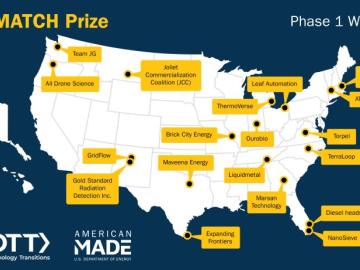
Three ORNL intellectual property projects with industry partners have advanced in DOE's Office of Technology Transitions Making Advanced Technology Commercialization Harmonized, or Lab MATCH, prize, which encourages entrepreneurs to find actionable pathways that bring lab-developed intellectual property to market.

Scientists at ORNL have developed 3-D-printed collimator techniques that can be used to custom design collimators that better filter out noise during different types of neutron scattering experiments
ORNL scientists have determined how to avoid costly and potentially irreparable damage to large metallic parts fabricated through additive manufacturing, also known as 3D printing, that is caused by residual stress in the material.