Filter News
Area of Research
News Topics
- (-) 3-D Printing/Advanced Manufacturing (116)
- (-) Software (1)
- Advanced Reactors (33)
- Artificial Intelligence (84)
- Big Data (50)
- Bioenergy (88)
- Biology (96)
- Biomedical (58)
- Biotechnology (21)
- Buildings (54)
- Chemical Sciences (59)
- Clean Water (29)
- Climate Change (94)
- Composites (25)
- Computer Science (183)
- Coronavirus (46)
- Critical Materials (24)
- Cybersecurity (35)
- Decarbonization (73)
- Education (3)
- Element Discovery (1)
- Emergency (2)
- Energy Storage (106)
- Environment (192)
- Exascale Computing (35)
- Fossil Energy (5)
- Frontier (40)
- Fusion (53)
- Grid (60)
- High-Performance Computing (83)
- Hydropower (11)
- Irradiation (3)
- Isotopes (47)
- ITER (7)
- Machine Learning (44)
- Materials (140)
- Materials Science (134)
- Mathematics (6)
- Mercury (12)
- Microelectronics (2)
- Microscopy (50)
- Molten Salt (8)
- Nanotechnology (60)
- National Security (58)
- Net Zero (11)
- Neutron Science (129)
- Nuclear Energy (105)
- Partnerships (40)
- Physics (59)
- Polymers (31)
- Quantum Computing (30)
- Quantum Science (65)
- Renewable Energy (2)
- Security (24)
- Simulation (45)
- Space Exploration (24)
- Statistics (3)
- Summit (57)
- Sustainable Energy (120)
- Transformational Challenge Reactor (7)
- Transportation (93)
Media Contacts
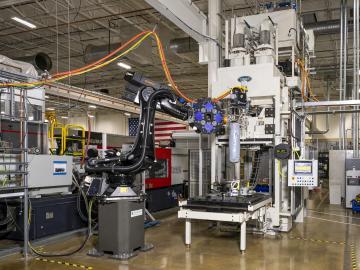
An Oak Ridge National Laboratory-developed advanced manufacturing technology, AMCM, was recently licensed by Orbital Composites and enables the rapid production of composite-based components, which could accelerate the decarbonization of vehicles

Researchers at the Department of Energy’s Oak Ridge National Laboratory, in collaboration with NASA, are taking additive manufacturing to the final frontier by 3D printing the same kind of wheel as the design used by NASA for its robotic lunar rover, demonstrating the technology for specialized parts needed for space exploration.
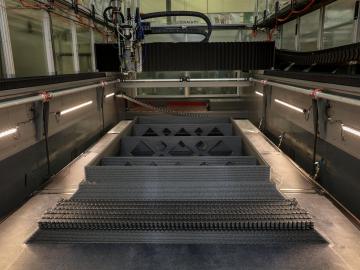
Oak Ridge National Laboratory researchers have conducted a comprehensive life cycle, cost and carbon emissions analysis on 3D-printed molds for precast concrete and determined the method is economically beneficial compared to conventional wood molds.
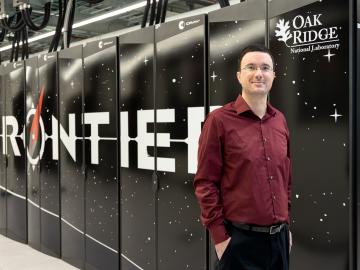
The Exascale Small Modular Reactor effort, or ExaSMR, is a software stack developed over seven years under the Department of Energy’s Exascale Computing Project to produce the highest-resolution simulations of nuclear reactor systems to date. Now, ExaSMR has been nominated for a 2023 Gordon Bell Prize by the Association for Computing Machinery and is one of six finalists for the annual award, which honors outstanding achievements in high-performance computing from a variety of scientific domains.
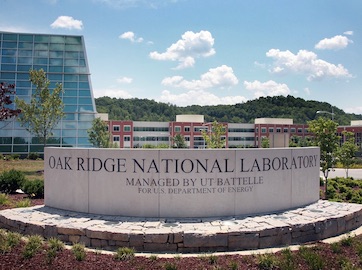
The Department of Energy’s Office of Science has selected three ORNL research teams to receive funding through DOE’s new Biopreparedness Research Virtual Environment initiative.
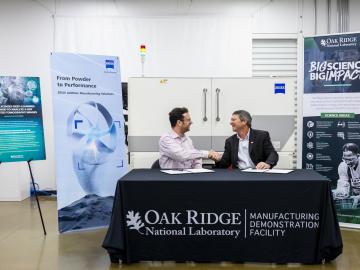
A licensing agreement between the Department of Energy’s Oak Ridge National Laboratory and research partner ZEISS will enable industrial X-ray computed tomography, or CT, to perform rapid evaluations of 3D-printed components using ORNL’s machine

Technologies developed by researchers at ORNL have received six 2023 R&D 100 Awards.
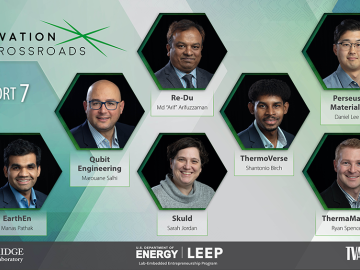
Seven entrepreneurs will embark on a two-year fellowship as the seventh cohort of Innovation Crossroads kicks off this month at ORNL. Representing a range of transformative energy technologies, Cohort 7 is a diverse class of innovators with promising new companies.

Yarom Polsky, director of the Manufacturing Science Division, or MSD, at the Department of Energy’s Oak Ridge National Laboratory, has been elected a Fellow of the American Society of Mechanical Engineers, or ASME.
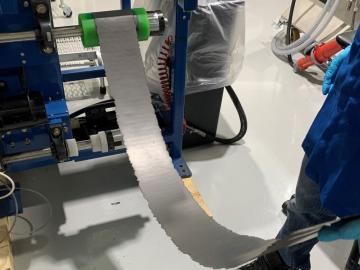
Early experiments at the Department of Energy’s Oak Ridge National Laboratory have revealed significant benefits to a dry battery manufacturing process. This eliminates the use of solvents and is more affordable, while showing promise for delivering a battery that is durable, less weighed down by inactive elements, and able to maintain a high capacity after use.