
Filter News
Area of Research
- Advanced Manufacturing (4)
- Biological Systems (2)
- Biology and Environment (136)
- Biology and Soft Matter (1)
- Clean Energy (118)
- Climate and Environmental Systems (5)
- Computational Biology (2)
- Computational Engineering (2)
- Computer Science (1)
- Electricity and Smart Grid (1)
- Functional Materials for Energy (1)
- Fusion and Fission (8)
- Fusion Energy (1)
- Isotope Development and Production (1)
- Isotopes (10)
- Materials (65)
- Materials for Computing (9)
- Mathematics (1)
- National Security (12)
- Neutron Science (28)
- Nuclear Science and Technology (9)
- Quantum information Science (2)
- Supercomputing (75)
- Transportation Systems (1)
News Topics
- (-) Bioenergy (91)
- (-) Biomedical (58)
- (-) Composites (26)
- (-) Decarbonization (79)
- (-) Environment (194)
- (-) Frontier (42)
- (-) Microscopy (51)
- (-) Space Exploration (25)
- 3-D Printing/Advanced Manufacturing (121)
- Advanced Reactors (34)
- Artificial Intelligence (91)
- Big Data (53)
- Biology (98)
- Biotechnology (22)
- Buildings (57)
- Chemical Sciences (63)
- Clean Water (29)
- Climate Change (99)
- Computer Science (187)
- Coronavirus (46)
- Critical Materials (26)
- Cybersecurity (35)
- Education (4)
- Element Discovery (1)
- Emergency (2)
- Energy Storage (108)
- Exascale Computing (37)
- Fossil Energy (5)
- Fusion (54)
- Grid (62)
- High-Performance Computing (84)
- Hydropower (11)
- Irradiation (3)
- Isotopes (53)
- ITER (7)
- Machine Learning (47)
- Materials (144)
- Materials Science (140)
- Mathematics (7)
- Mercury (12)
- Microelectronics (3)
- Molten Salt (8)
- Nanotechnology (60)
- National Security (61)
- Net Zero (13)
- Neutron Science (131)
- Nuclear Energy (108)
- Partnerships (44)
- Physics (61)
- Polymers (33)
- Quantum Computing (34)
- Quantum Science (69)
- Renewable Energy (2)
- Security (24)
- Simulation (47)
- Software (1)
- Statistics (3)
- Summit (57)
- Sustainable Energy (125)
- Transformational Challenge Reactor (7)
- Transportation (97)
Media Contacts

Hilda Klasky, an R&D staff member in the Scalable Biomedical Modeling group at ORNL, has been selected as a senior member of the Association of Computing Machinery, or ACM.

The founder of a startup company who is working with ORNL has won an Environmental Protection Agency Green Chemistry Challenge Award for a unique air pollution control technology.

Raina Setzer knows the work she does matters. That’s because she’s already seen it from the other side. Setzer, a radiochemical processing technician in Oak Ridge National Laboratory’s Isotope Processing and Manufacturing Division, joined the lab in June 2023.
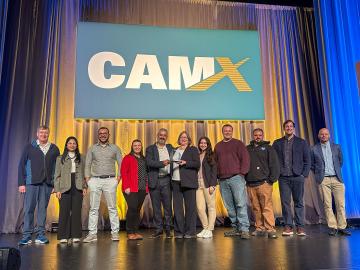
The Hub & Spoke Sustainable Materials & Manufacturing Alliance for Renewable Technologies, or SM2ART, program has been honored with the composites industry’s Combined Strength Award at the Composites and Advanced Materials Expo, or CAMX, 2023 in Atlanta. This distinction goes to the team that applies their knowledge, resources and talent to solve a problem by making the best use of composites materials.
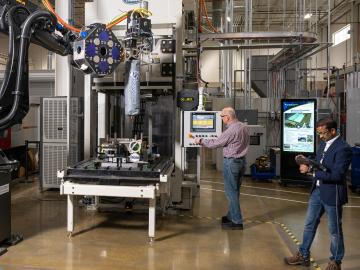
Researchers at ORNL are extending the boundaries of composite-based materials used in additive manufacturing, or AM. ORNL is working with industrial partners who are exploring AM, also known as 3D printing, as a path to higher production levels and fewer supply chain interruptions.
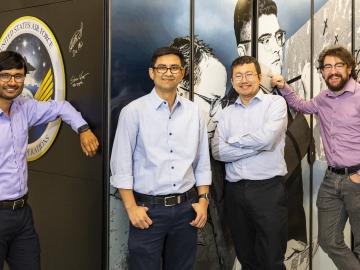
ORNL researchers tested a new modeling framework that simulates a flood event from precipitation to inundation.

Oak Ridge National Laboratory scientists identified a gene “hotspot” in the poplar tree that triggers dramatically increased root growth. The discovery supports development of better bioenergy crops and other plants that can thrive in difficult conditions while storing more carbon belowground.

In fiscal year 2023 — Oct. 1–Sept. 30, 2023 — Oak Ridge National Laboratory was awarded more than $8 million in technology maturation funding through the Department of Energy’s Technology Commercialization Fund, or TCF.

Little of the mixed consumer plastics thrown away or placed in recycle bins actually ends up being recycled. Nearly 90% is buried in landfills or incinerated at commercial facilities that generate greenhouse gases and airborne toxins. Neither outcome is ideal for the environment.

Researchers at the Department of Energy’s Oak Ridge National Laboratory, in collaboration with NASA, are taking additive manufacturing to the final frontier by 3D printing the same kind of wheel as the design used by NASA for its robotic lunar rover, demonstrating the technology for specialized parts needed for space exploration.