
Filter News
Area of Research
- Advanced Manufacturing (3)
- Biology and Environment (59)
- Biology and Soft Matter (1)
- Clean Energy (43)
- Climate and Environmental Systems (1)
- Computational Biology (1)
- Fusion and Fission (4)
- Fusion Energy (1)
- Isotopes (16)
- Materials (34)
- Materials for Computing (4)
- National Security (15)
- Neutron Science (9)
- Nuclear Science and Technology (5)
- Quantum information Science (2)
- Supercomputing (26)
News Type
News Topics
- (-) 3-D Printing/Advanced Manufacturing (36)
- (-) Biology (57)
- (-) Climate Change (47)
- (-) Composites (6)
- (-) Cybersecurity (14)
- (-) Isotopes (26)
- (-) Materials (40)
- (-) Microscopy (20)
- (-) Molten Salt (1)
- (-) Space Exploration (12)
- Advanced Reactors (8)
- Artificial Intelligence (45)
- Big Data (21)
- Bioenergy (49)
- Biomedical (28)
- Biotechnology (10)
- Buildings (17)
- Chemical Sciences (21)
- Clean Water (14)
- Computer Science (81)
- Coronavirus (17)
- Critical Materials (1)
- Decarbonization (43)
- Education (1)
- Emergency (2)
- Energy Storage (28)
- Environment (100)
- Exascale Computing (24)
- Fossil Energy (4)
- Frontier (23)
- Fusion (29)
- Grid (23)
- High-Performance Computing (42)
- Hydropower (5)
- ITER (2)
- Machine Learning (21)
- Materials Science (43)
- Mathematics (5)
- Mercury (7)
- Microelectronics (2)
- Nanotechnology (16)
- National Security (34)
- Net Zero (8)
- Neutron Science (47)
- Nuclear Energy (52)
- Partnerships (15)
- Physics (28)
- Polymers (8)
- Quantum Computing (20)
- Quantum Science (30)
- Renewable Energy (1)
- Security (10)
- Simulation (30)
- Software (1)
- Summit (30)
- Sustainable Energy (43)
- Transformational Challenge Reactor (3)
- Transportation (27)
Media Contacts

In the race to identify solutions to the COVID-19 pandemic, researchers at the Department of Energy’s Oak Ridge National Laboratory are joining the fight by applying expertise in computational science, advanced manufacturing, data science and neutron science.
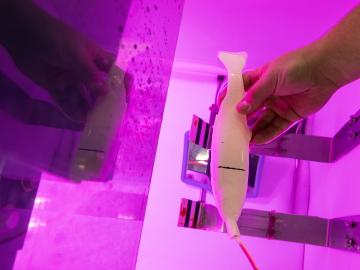
Hydropower developers must consider many factors when it comes time to license a new project or renew an existing one: How can environmental impacts be mitigated, including to fish populations?

Scientists at the Department of Energy’s Oak Ridge National Laboratory have developed a new method to peer deep into the nanostructure of biomaterials without damaging the sample. This novel technique can confirm structural features in starch, a carbohydrate important in biofuel production.
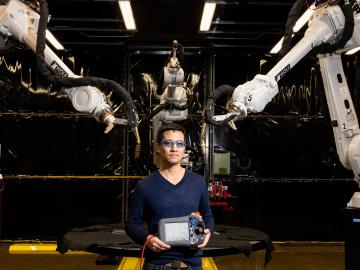
Peter Wang is focused on robotics and automation at the Department of Energy’s Manufacturing Demonstration Facility at ORNL, working on high-profile projects such as the MedUSA, a large-scale hybrid additive manufacturing machine.
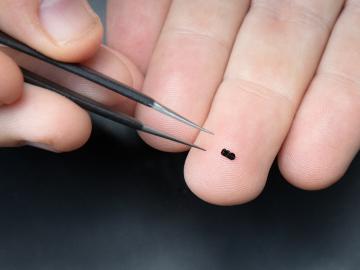
Liam Collins was drawn to study physics to understand “hidden things” and honed his expertise in microscopy so that he could bring them to light.

The type of vehicle that will carry people to the Red Planet is shaping up to be “like a two-story house you’re trying to land on another planet.
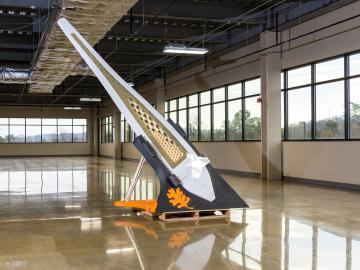
In the shifting landscape of global manufacturing, American ingenuity is once again giving U.S companies an edge with radical productivity improvements as a result of advanced materials and robotic systems developed at the Department of Energy’s Manufacturing Demonstration Facility (MDF) at Oak Ridge National Laboratory.
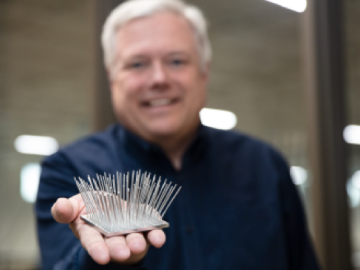
When Scott Smith looks at a machine tool, he thinks not about what the powerful equipment used to shape metal can do – he’s imagining what it could do with the right added parts and strategies. As ORNL’s leader for a newly formed group, Machining and Machine Tool Research, Smith will have the opportunity to do just that.
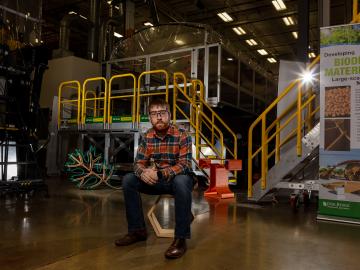
Alex Roschli is no stranger to finding himself in unique situations. After all, the early career researcher in ORNL’s Manufacturing Systems Research group bears a last name that only 29 other people share in the United States, and he’s certain he’s the only Roschli (a moniker that hails from Switzerland) with the first name Alex.
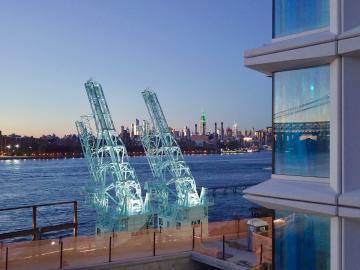
A residential and commercial tower under development in Brooklyn that is changing the New York City skyline has its roots in research at the Department of Energy’s Oak Ridge National Laboratory.